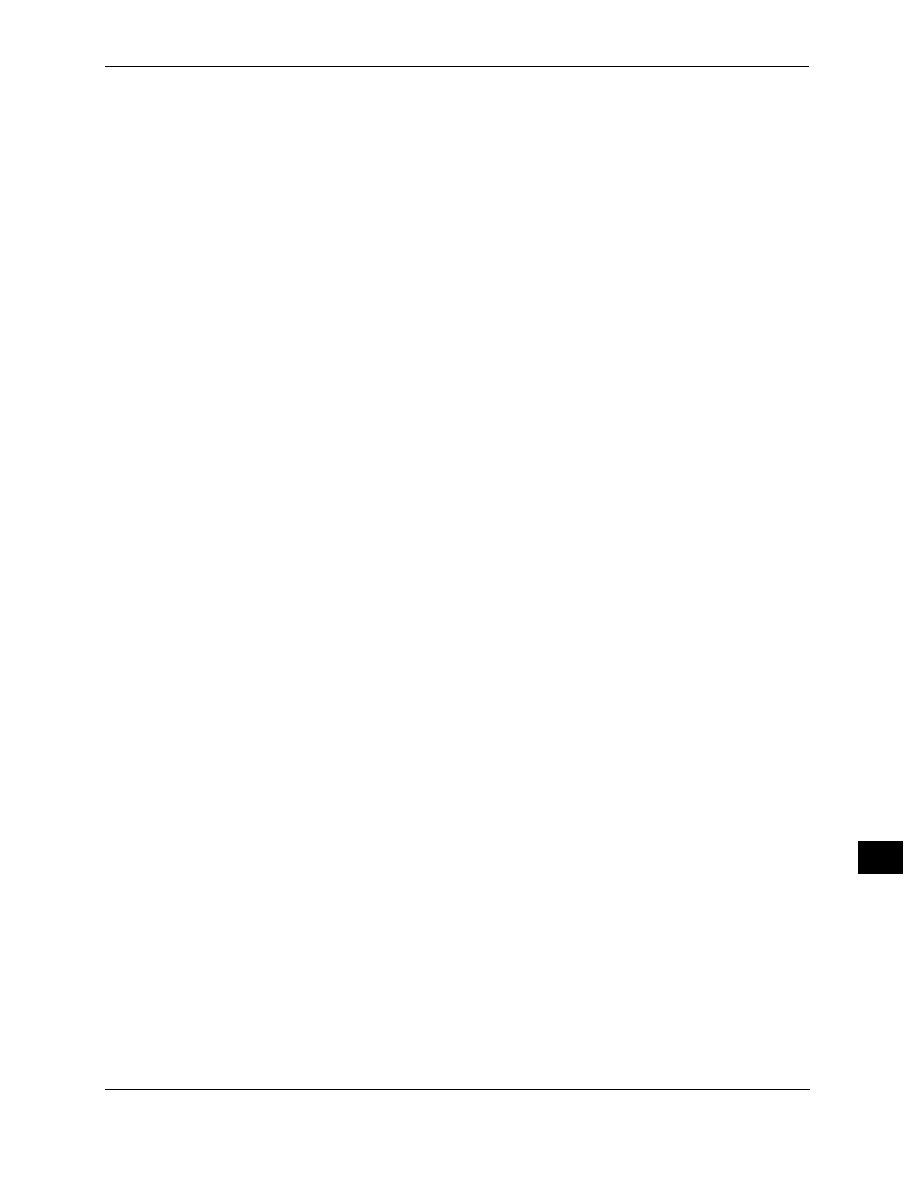
Introduction
MOTOROLA
JTAG Port
17-3
Preliminary
17
17.1 Introduction
This chapter describes the DSP56F800E core-based family of chips, providing board and
chip-level debugging and high-density circuit board testing specific to Joint Test Action
Group (JTAG).
The DSP56853/854/855/857/858 provides board and chip-level testing capability through
two on-chip modules, both accessed through the JTAG port/EOnCE module interface:
Enhanced On-chip Emulation (EOnCE) module
Test Access Port (TAP) and 16-state controller, also known as the JTAG port
Presence of the JTAG port/EOnCE module interface permits insertion of the DSP chip
into a target system while retaining debug control. This capability is especially important
for devices without an external bus, because it eliminates the need for a costly cable to
bring out the footprint of the chip required by a traditional emulator system.
The Enhanced OnCE (EOnCE) module is a Motorola-designed module used in Digital
Signal Processor (DSP) chips to debug application software employed with the chip. The
port is a separate on-chip block allowing non-intrusive DSP interaction with accessibility
through the pins of the JTAG interface. The EOnCE module makes it possible to examine
registers, memory, or on-chip peripherals’ contents in a special debug environment. This
avoids sacrificing any user-accessible, on-chip resources to perform debugging
procedures. Please refer to DSP56F800E Core-Based Reference Manual for details about
implementation of the DSP5685x EOnCE module.
The JTAG port is a dedicated user-accessible TAP compatible with the IEEE
1149.1a-1993 Standard Test Access Port and Boundary Scan Architecture. Problems
associated with testing high-density circuit boards have led to the development of this
proposed standard under the sponsorship of the Test Technology Committee of IEEE and
the JTAG. DSP5685x supports circuit board test strategies based on this standard.
Six dedicated pins interface to the TAP containing a 16-state controller. The TAP uses a
boundary scan technique to test the interconnections between integrated circuits after they
are assembled onto a Printed Circuit Board (PCB). Boundary scans allow observation and
control signal levels at each component pin through a Shift register placed next to each
pin. This is important for testing continuity and determining if pins are stuck at a one or
zero level.