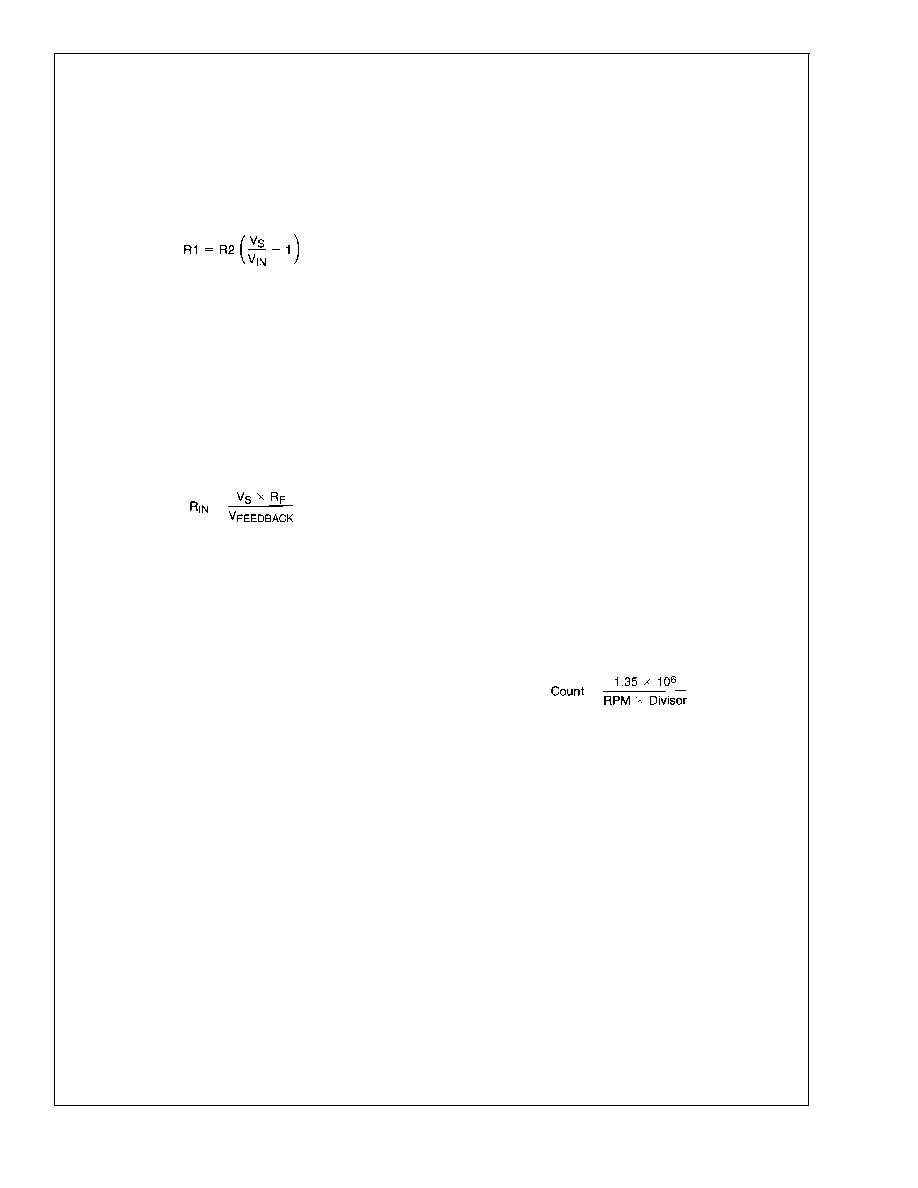
Functional Description (Continued)
of the voltage, yet leaves headroom for upward excursions
from the supply of about 25%. To simplify the process of re-
sistor selection, set the value of R2 first. Select a value for
R2 between 10 k
and 100 k. This is low enough to avoid
errors due to input leakage currents yet high enough to both
protect the inputs under overdrive conditions as well as mini-
mize loading of the source. Then select R1 to provide a 3V
input according to:
The negative inputs provide inverting op amps with
non-inverting inputs connected to ground. The output of
these op amps are designed to only drive the input of the
LM78 and their associated feedback loops. Avoid heavy
loading, long lines, and capacitive loading with these op
amps. Additional loading may cause oscillations and thus er-
roneous readings. The optimum feedback resistor (resistor
from Feedback to -IN pin) value is approximately 60 k
,
based on the op amp nominal output current rating of 50 A
at an output voltage of 3V. Locate the feedback resistors as
close as possible to the LM79. The recommended range for
R
IN is from 30 k to 300 k.
Select R
IN according to:
The analog inputs have internal diodes that clamp inputs ex-
ceeding the power supply and ground. Exceeding any ana-
log input has no detrimental effect on other channels. The in-
put diodes will also clamp voltages appearing at the inputs of
an un-powered LM79. External resistors should be included
to limit input currents to the values given in the ABSOLUTE
MAXIMUM RATINGS for Input Current At Any Pin. Inputs
with the attenuator networks will usually meet these require-
ments. If it is possible for inputs without attenuators (such as
the 2.5V or 3.3V supplies) to be turned on while LM79 is
powered off, additional resistors of about 10 k
should be
added in series with the inputs to limit the input current.
5.0 LAYOUT AND GROUNDING
Analog inputs will provide best accuracy when referred to the
AGND pin. A separate, low-impedance ground plane for ana-
log ground, which provides a ground point for the voltage di-
viders and analog components, will provide best perfor-
mance but is not mandatory. Analog components such as
voltage dividers and feedback resistors should be located
physically as close as possible to the LM79.
The power supply bypass, the parallel combination of 10 F
(electrolytic or tantalum) and 0.1 F (ceramic) bypass ca-
pacitors connected between pin 12 and ground, should also
be located as close as possible to the LM79.
6.0 FAN INPUTS
Inputs are provided for signals from fans equipped with ta-
chometer outputs. These are logic-level inputs with an ap-
proximate threshold of 1.4V. Signal conditioning in the LM79
accommodates the slow rise and fall times typical of fan ta-
chometer outputs. The maximum input signal range is 0 to
V
CC. In the event these inputs are supplied from fan outputs
which exceed 0 to V
CC, either resistive division or diode
clamping must be included to keep inputs within an accept-
able range, as shown in
Figure 9. R2 is selected so that it
does not develop excessive voltage due to input leakage. R1
is selected based on R2 to provide a minimum input of 2V
and a maximum of V
CC. R1 should be as low as possible to
provide the maximum possible input up to V
CC for best noise
immunity. Alternatively, use a shunt reference or zener diode
to clamp the input level.
If fans can be powered while the power to the LM79 is off,
the LM79 inputs will provide diode clamping. Limit input cur-
rent to the Input Current at Any Pin specification shown in the
ABSOLUTE MAXIMUM RATINGS section. In most cases,
open collector outputs with pull-up resistors inherently limit
this current. If this maximum current could be exceeded, ei-
ther a larger pull up resistor should be used or resistors con-
nected in series with the fan inputs.
The Fan Inputs gate an internal 22.5 kHz oscillator for one
period of the Fan signal into an 8-bit counter (maximum
count = 255). The default divisor, located in the VID/Fan Di-
visor Register, is set to 2 (choices are 1, 2, 4, and 8) provid-
ing a nominal count of 153 for a 4400 rpm fan with two
pulses per revolution. Typical practice is to consider 70% of
normal RPM a fan failure, at which point the count will be
219.
Determine the fan count according to:
Note that Fan 1 and Fan 2 Divisors are programmable via
the VID/Fan Divisor Register. Fan 3 is not adjustable, and its
Divisor is always set to 2.
Fans that provide only one pulse per revolution would re-
quire a divisor set twice as high as fans that provide two
pulses, thus maintaining a nominal fan count of 153. There-
fore, the divisor should be set to 4 for a fan that provides 1
pulse per revolution with a nominal RPM of 4400.
LM79
www.national.com
17