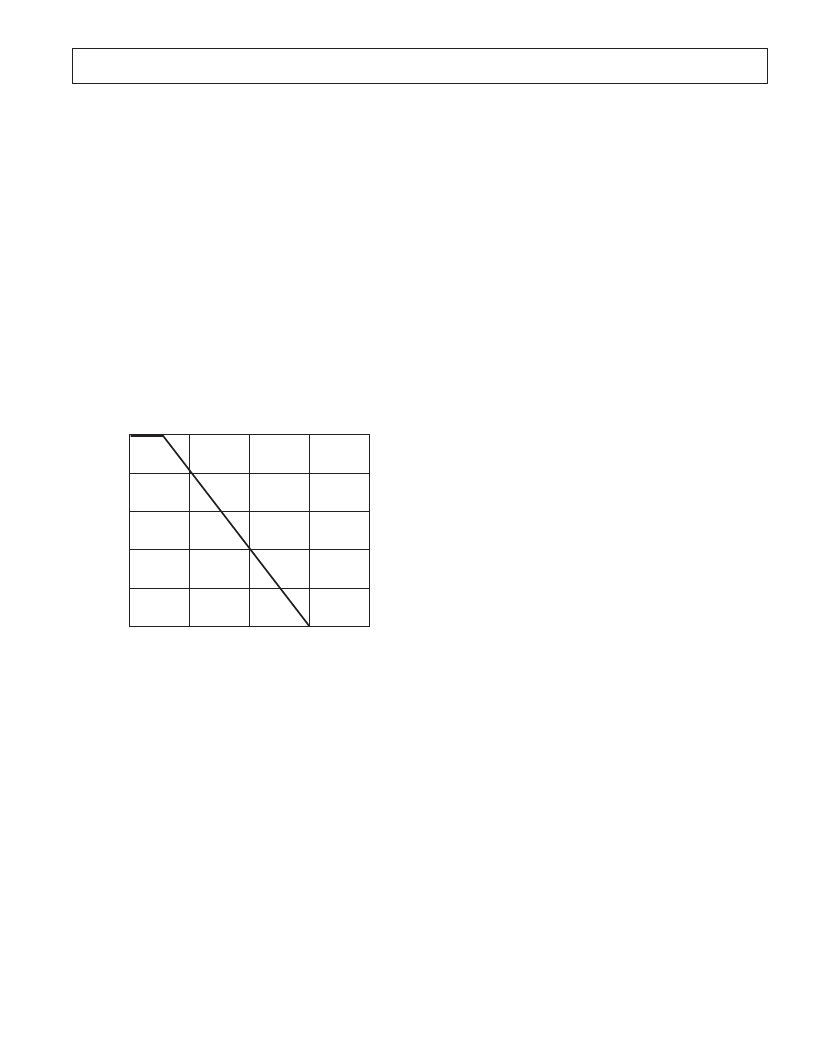
REV. C
ADN8830
–13–
Using TEMPOUT to Measure Temperature
The TEMPOUT pin is a voltage that is proportional to the
difference between the target temperature and the measured
thermistor temperature. The full equation for the voltage at
TEMPOUT
is
×
(
TEMPOUT
The voltage range of
TEMPOUT
is 0 V to 3.0 V and is inde-
pendent of power supply voltage.
Setting the Maximum TEC Voltage and Current
The ADN8830 can be programmed for a maximum output volt-
age to protect the TEC. A voltage from 0 V to 1.5 V applied to
the VLIM (Pin 15) input to the ADN8830 sets the maximum
TEC voltage, V
TEC, MAX
. This voltage can be set with either a
resistor divider or from a DAC. Because the output of the
ADN8830 is bidirectional, this voltage sets both the upper
and lower limits of the TEC voltage. The equation governing
V
TEC, MAX
is given in Equation 17 and the graph of this equation
is shown in Figure 12.
=
(
THERMIN
TEMPSET
=
+
)
1 5
.
3
–
(16)
V
V
VLIM
TEC MAX
,
.
–
)
×
1 5
4
(17)
VLIM (V)
5
00
2.0
0.5
V
T
(
1.0
1.5
4
3
2
1
Figure 12. VLIM Voltage vs. Maximum TEC Voltage
If the supply voltage is lower than V
TEC, MAX
, the maximum TEC
voltage will obviously be equal to the supply voltage. The voltage
to VLIM should not exceed 1.5 V since this causes improper
operation of the output voltage limiting circuitry. Setting VLIM to
1.5 V can be used to deactivate the TEC current without
shutting down the ADN8830 in the event of a system failure. If a
maximum TEC voltage is not required, VLIM should be con-
nected to ground. It is not advisable to leave VLIM floating as
this would cause unpredictable output behavior.
This feature should be used to limit the maximum output current
to the TEC as specified in the TEC data sheet. For example, if
the maximum TEC voltage is specified at 2 V, VLIM should be
set to 1 V. The maximum output voltage is then set to
±
2 V.
Output Driver Amplifiers
The output voltage across the TEC as measured from Pin 19 to
Pin 9 can be monitored at Pin 16. This is labeled as VTEC in
the typical application schematic in Figure 1. The voltage at
VTEC can vary from 0 V to 3 V independent of the power
supply voltage. Its equation is given as
×
(
VTEC
V
V
OUT A
OUT B
=
)
+
0 25
.
1 5
.
–
(18)
where
V
OUT A
and
V
OUT B
are the voltages at Pins 19 and 9, respec-
tively. The ripple voltage at Pin 19 is filtered out internally and
does not appear at VTEC, leaving it as an accurate dc output of
the TEC voltage.
The TEC is driven with a differential voltage, allowing current
to flow in either direction through the TEC. This can provide
heat transfer either to or from the object being regulated without
the use of a negative voltage rail. The maximum output voltage
across the TEC is set by the voltage at VLIM (Pin 15). Refer to
the Setting the Maximum TEC Voltage and Current section for
details on this operation. With VLIM set to ground, the maximum
output voltage is the power supply voltage, V
DD
.
To achieve a differential output, the ADN8830 has two separate
output stages. OUT A is a switched output or pulse-width
modulated (PWM) amplifier, and OUT B is a high gain linear
amplifier. Although they achieve the same result, to provide
constant voltage and high current, their operation is different.
The exact equations for the two outputs are
×
(
×
(
–
14
where
COMPOUT
is the voltage at Pin 13. The voltage at
COMPOUT
is determined by the compensation network that is
fed by the input amplifier, which receives its input voltage from
TEMPSET and THERMIN. Equation 20 is valid only in the
linear region of the linear amplifier. OUT B has a lower limit of
0 V and an upper limit of the power supply.
Because the COMPOUT voltage is not readily known, Equa-
tion 20 can be rewritten in terms of the TEC voltage, VTEC,
which is defined as OUT B
–
OUT A.
VTEC
=
×
+
4
1 5
OUT A
COMPOUT
OUT B
=
)
+
4
1 5
–
.
(19)
OUT B
COMPOUT
=
)
+
–
.
1 5
.
1 5
(20)
OUT B
(21)
In Figure 1, Pins 10 and 11 provide the gate drive for Q3 and Q4,
which complete the linear output amplifier. This output voltage
is fed back to Pin 9 (OUT B) to close its loop. The gate-to-drain
capacitance of Q3 and Q4 provide the compensation for the
linear amplifier. If using the recommended FDW2520C transistors,
it will be necessary to add an additional 2.2 nF of capacitance
from the gate to the drain of the PMOS transistor to maintain
stability. A 3.3 nF capacitor should also be connected from the
drain to ground to prevent small oscillations when there is very
little or no current through the TEC.
These extra capacitors are specified only when using FDW2520C
transistors in the linear amplifier. If other transistors are used,
these values may need to be adjusted. To ensure the linear
amplifier is stable, the total gate-to-source capacitance for both
Q3 and Q4 should be at least 2.5 nF. Refer to the transistor
’
s
data sheet for its typical gate-to-drain capacitance values.
The output of the linear amplifier is proportional to the voltage
at Pin 13 (COMPOUT). Because the linear amplifier operates
with a gain of 14, its output will typically be at either ground or
V
DD
if there is more than about 100 mA of current flowing
through the TEC. This ensures Q3 and Q4 will not be a domi-
nant source of power dissipation at high output currents.