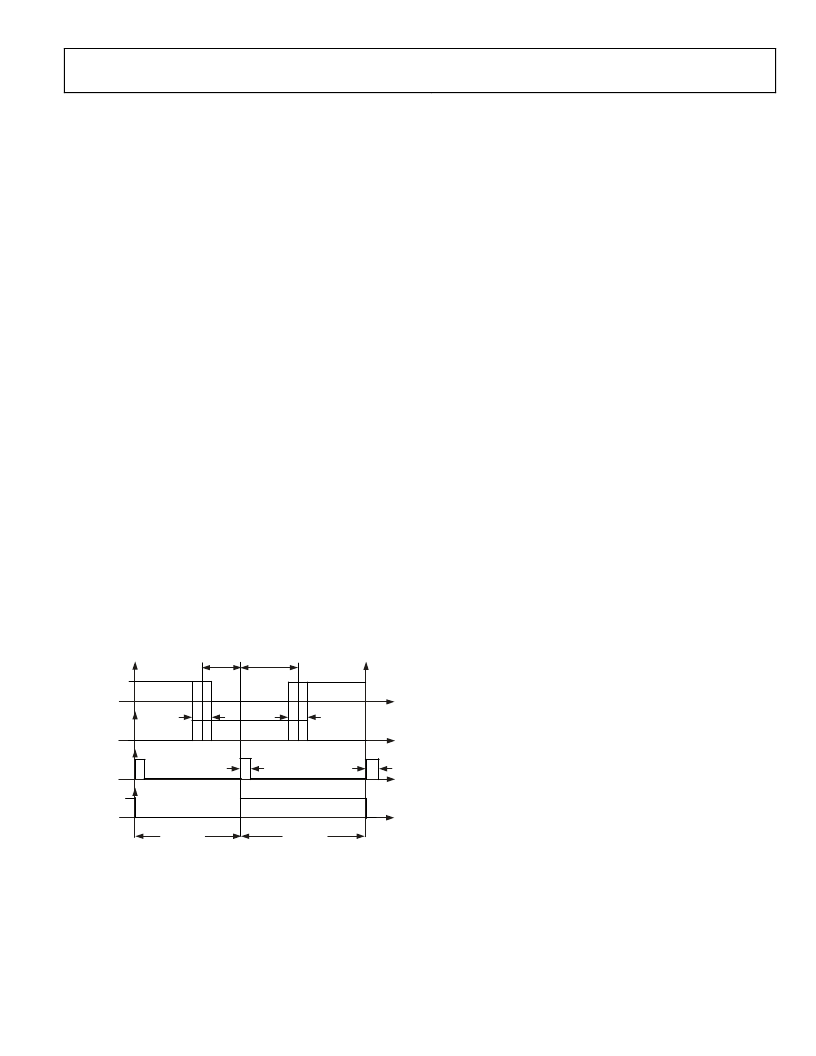
Preliminary Technical Data
ADuC702x Series
symmetrical output patterns.
Rev. PrB | Page 45 of 80
Also shown is the PWMSYNC pulse and Bit 0 of the PWMSTA
register that indicates whether operation is in the first or
second half cycle of the PWM period.
The resultant on-times of the PWM signals over the full PWM
period (two half periods) produced by the timing unit can be
written as:
T
0H
= 2 x (PWMCH0 - PWMDAT1) x t
CORE
T
0L
= 2 x (PWMDAT0 – PWMCH0 – PWMDAT1) x t
CORE
And the corresponding duty cycles:
d
0H
= T
0H
/ Ts = (
PWMCH0 – PWMDAT1) /
PWMDAT0
d
0L
= T
0L
/ Ts = (PWMDAT0 – PWMCH0 – PWMDAT1)
/
PWMDAT0
The minimum permissible T
0H
and T
0L
values are zero,
corresponding to a 0% duty cycle. In a similar fashion, the
maximum value is T
S
, corresponding to a 100% duty cycle.
The output signals from the timing unit for operation in double
update mode are shown in Figure 23. This illustrates a
completely general case where the switching frequency, dead
time and duty cycle are all changed in the second half of the
PWM period. Of course, the same value for any or all of these
quantities could be used in both halves of the PWM cycle.
However, it can be seen that there is no guarantee that
symmetrical PWM signals will be produced by the timing unit
in double update mode. Additionally, it is seen that the dead
time is inserted into the PWM signals in the same way as in the
single update mode.
PWMCH01
2 x
PWMDAT12
PWMCH02
0H
PWMSTA (0)
0L
PWMDAT01
PWMDAT02
2 x
PWMDAT11
PWMSYNC
PWMDAT22+1
PWMDAT21+1
Figure 23: Typical PWM outputs of the Three-phase timing unit in double
update mode
In general the on-times of the PWM signals in double update
mode can be defined as:
T
0H
= (PWMCH0
1
+ PWMCH0
2
– PWMDAT1
1
– PWMDAT1
2
)
x t
CORE
T
0L
= (PWMDAT0
1
+ PWMDAT0
2
- PWMCH0
1
- PWMCH0
2
–
PWMDAT1
1
– PWMDAT1
2
) x t
CORE
where the subscript 1 refers to the value of that register during
the first half cycle and the subscript 2 refers to the value during
the second half cycle. The corresponding duty cycles are:
d
0H
= T
0H
/ Ts = (PWMCH0
1
+ PWMCH0
2
– PWMDAT1
1
–
PWMDAT1
2
) / (PWMDAT0
1
+ PWMDAT0
2
)
d
0L
= T
0L
/Ts = (PWMDAT0
1
+ PWMDAT0
2
- PWMCH0
1
-
PWMCH0
2
– PWMDAT1
1
– PWMDAT1
2
) / (PWMDAT0
1
+
PWMDAT0
2
)
since for the completely general case in double update mode,
the switching period is given by:
Ts =
(PWMDAT0
1
+ PWMDAT0
2
) x t
CORE
Again, the values of T
0H
and T
0L
are constrained to lie between
zero and T
S
.
PWM signals similar to those illustrated in Figure 22 and
Figure 23 can be produced on the 1H, 1L, 2H and 2L outputs by
programming the PWMCH1 and PWMCH2 registers in a
manner identical to that described for PWMCH0. The PWM
controller does not produce any PWM outputs until all of the
PWMDAT0, PWMCH0, PWMCH1 and PWMCH2 registers
have been written to at least once. Once these registers have
been written, internal counting of the timers in the three-phase
timing unit is enabled. Writing to the PWMDAT0 register
starts the internal timing of the main PWM timer. Provided the
PWMDAT0 register is written prior to the PWMCH0,
PWMCH1 and PWMCH2 registers in the initialisation, the
first PWMSYNC pulse and interrupt (if enabled) appear 1.5 x
t
CORE
x PWMDAT0 seconds after the initial write to the
PWMDAT0 register in single update mode. In double update
mode, the first PWMSYNC pulse appears after PWMDAT0 x
t
CORE
seconds.
Output Control Unit
The operation of the Output Control Unit is controlled by the
9-bit read/write PWMEN register. This register controls two
distinct features of the Output Control Unit that are directly
useful in the control of ECM or BDCM. The PWMEN register
contains three crossover bits, one for each pair of PWM outputs.
Setting Bit 8 of the PWMEN register enables the crossover
mode for the 0H/0L pair of PWM signals, setting Bit 7 enables
crossover on the 1H/1L pair of PWM signals and setting Bit 6
enables crossover on the 2H/2L pair of PWM signals. If
crossover mode is enabled for any pair of PWM signals, the
high-side PWM signal from the timing unit (0H, for example) is
diverted to the associated low-side output of the Output
Control Unit so that the signal will ultimately appear at the 0L
pin. Of course, the corresponding low-side output of the Timing
Unit is also diverted to the complementary high-side output of