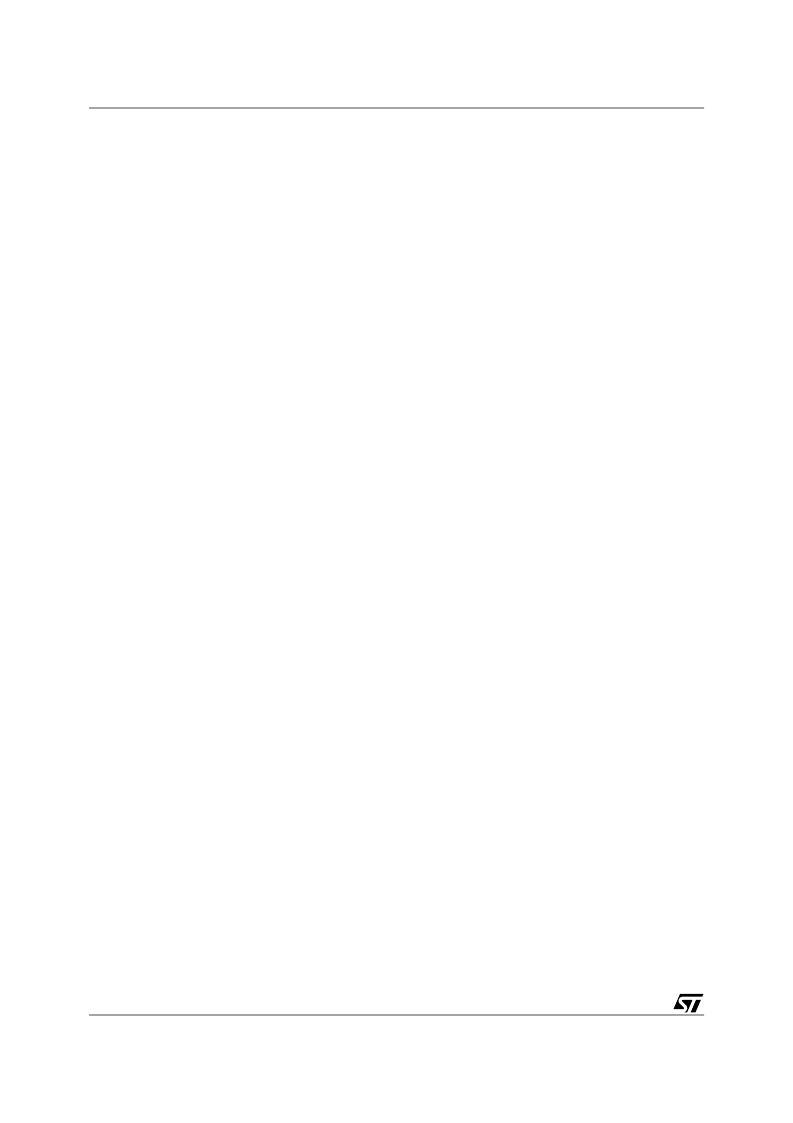
L6711
28/38
15 DRIVER SECTION
The integrated high-current drivers allow using different types of power MOS (also multiple MOS to reduce
the equivalent R
dsON
), maintaining fast switching transition.
The drivers for the high-side mosfets use BOOTx pins for supply and PHASEx pins for return. The drivers
for the low-side mosfets use VCCDRx pin for supply and PGNDx pin for return. A minimum voltage of 4.6V
at VCCDRx pin is required to start operations of the device. VCCDRx pins must be connected together.
The controller embodies a sophisticated anti-shoot-through system to minimize low side body diode con-
duction time maintaining good efficiency saving the use of Schottky diodes: when the high-side mosfet
turns off, the voltage on its source begins to fall; when the voltage reaches 2V, the low-side mosfet gate
drive is suddenly applied. When the low-side mosfet turns off, the voltage at LGATEx pin is sensed. When
it drops below 1V, the high-side mosfet gate drive is suddenly applied.
If the current flowing in the inductor is negative, the source of high-side mosfet will never drop. To allow
the turning on of the low-side mosfet even in this case, a watchdog controller is enabled: if the source of
the high-side mosfet doesn't drop for more than 240ns, the low side mosfet is switched on so allowing the
negative current of the inductor to recirculate. This mechanism allows the system to regulate even if the
current is negative.
The BOOTx and VCCDRx pins are separated from IC's power supply (VCC pin) as well as signal ground
(SGND pin) and power ground (PGNDx pin) in order to maximize the switching noise immunity. The sepa-
rated supply for the different drivers gives high flexibility in mosfet choice, allowing the use of logic-level mos-
fet. Several combination of supply can be chosen to optimize performance and efficiency of the application.
Power conversion input is also flexible; 5V, 12V bus or any bus that allows the conversion (See maximum
duty cycle limitations) can be chosen freely.
16 POWER DISSIPATION
Two main terms contribute in the device power dissipation: bias power and drivers' power. The first one de-
pends on the static consumption of the device through the supply pins and it is simply quantifiable as follow:
P
DC
= V
CC
· (I
CC
+ 3 · I
CCDRx
+ 3 · I
BOOTx
)
Drivers' power is the power needed by the driver to continuously switch on and off the external mosfets;
it is a function of the switching frequency and total gate charge of the selected mosfets. It can be quantified
considering that the total power P
SW
dissipated to switch the mosfets (easy calculable) is dissipated by
three main factors: external gate resistance (when present), intrinsic mosfet resistance and intrinsic driver
resistance. This last term is the important one to be determined to calculate the device power dissipation.
The total power dissipated to switch the mosfets results:
P
SW
= 3 · (Q
G_HS
· V
BOOT
+ Q
G_LS
· V
CCDR
) · F
SW
External gate resistors helps the device to dissipate the switching power since the same power P
SW
will
be shared between the internal driver impedance and the external resistor resulting in a general cooling
of the device.It is important to determine the device dissipated power in order to avoid the junction working
beyond its maximum operative temperature. Moreover, since the device has an exposed pad to better dis-
sipate the power, also the thermal resistance between junction and ambient is important.
Figure 16 shows the Switching Power for different kind of mosfets driven.