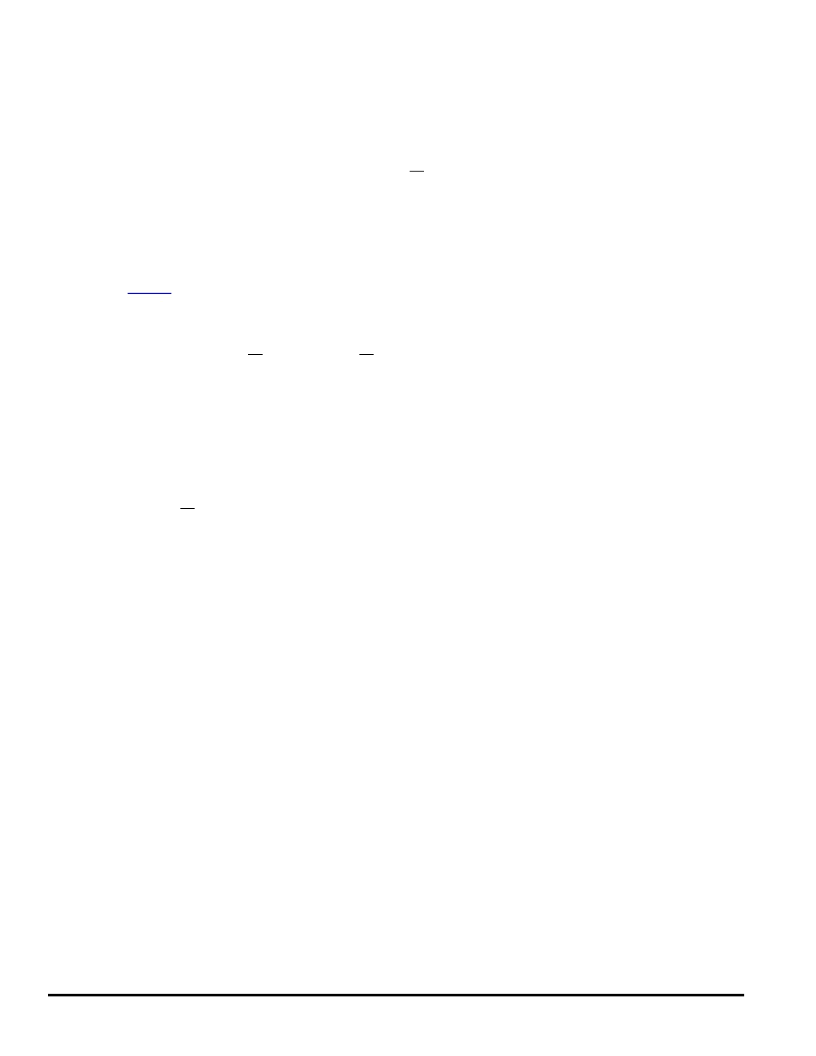
33887
18
MOTOROLA ANALOG INTEGRATED CIRCUIT DEVICE DATA
SYSTEM/APPLICATION INFORMATION
INTRODUCTION
Numerous protection and operational features (speed,
torque, direction, dynamic braking, PWM control, and closed-
loop control), in addition to the 5.0 A current capability, make
the 33887 a very attractive, cost-effective solution for
controlling a broad range of small DC motors. In addition, a pair
of 33887 devices can be used to control bipolar stepper motors.
The 33887 can also be used to excite transformer primary
windings with a switched square wave to produce secondary
winding AC currents.
As shown in
Figure 1
, Simplified Internal Block Diagram,
page 2, the 33887 is a fully protected monolithic H-Bridge with
Enable, Fault Status reporting, and High-Side current sense
feedback to accommodate closed-loop PWM control. For a DC
motor to run, the input conditions need be as follows: Enable
input logic HIGH, D1 input logic LOW,
D2
input logic HIGH,
FS
flag cleared (logic HIGH), one IN logic LOW and the other IN
logic HIGH (to define output polarity). The 33887 can execute
dynamic braking by simultaneously turning on either both high-
side
MOSFETs or both low-side MOSFETs in the output
H-Bridge; e.g., IN1 and IN2 logic HIGH or IN1 and IN2 logic
LOW.
The 33887 outputs are capable of providing a continuous DC
load current of 5.0 A from a 40 V V+ source. An internal charge
pump supports PWM frequencies to 10 kHz. An external pullup
resistor is required at the
FS
terminal for fault status reporting.
The 33887 has an analog feedback (current mirror) output
terminal (the FB terminal) that provides a constant-current
source ratioed to the active high-side MOSFET. This can be
used to provide “real time” monitoring of load current to facilitate
closed-loop operation for motor speed/torque control.
Two independent inputs (IN1 and IN2) provide control of the
two totem-pole half-bridge outputs. Two disable inputs (D1 and
D2
) provide the means to force the H-Bridge outputs to a high-
impedance state (all H-Bridge switches OFF). An EN terminal
controls an enable function that allows the 33887 to be placed
in a power-conserving sleep mode.
The 33887 has undervoltage shutdown with automatic
recovery, active current limiting, output short-circuit latch-OFF,
and overtemperature latch-OFF. An undervoltage shutdown,
output short-circuit latch-OFF, or overtemperature latch-OFF
fault condition will cause the outputs to turn OFF (i.e., become
high impedance or tri-stated) and the fault output flag to be set
LOW. Either of the Disable inputs or V+ must be “toggled” to
clear the fault flag.
Active current limiting is accomplished by a constant OFF-
time PWM method employing active current limiting threshold
triggering. The active current limiting scheme is unique in that it
incorporates a junction temperature-dependent current limit
threshold. This means the active current limiting threshold is
“ramped down” as the junction temperature increases above
160
°
C, until at 175
°
C the current will have been decreased to
about 4.0 A. Above 175
°
C,
the overtemperature shutdown
(latch-OFF) occurs. This combination of features allows the
device to remain in operation for 30 seconds at junction
temperatures above 150
°
C for nonrepetitive unexpected loads.
F
Freescale Semiconductor, Inc.
For More Information On This Product,
Go to: www.freescale.com
n
.