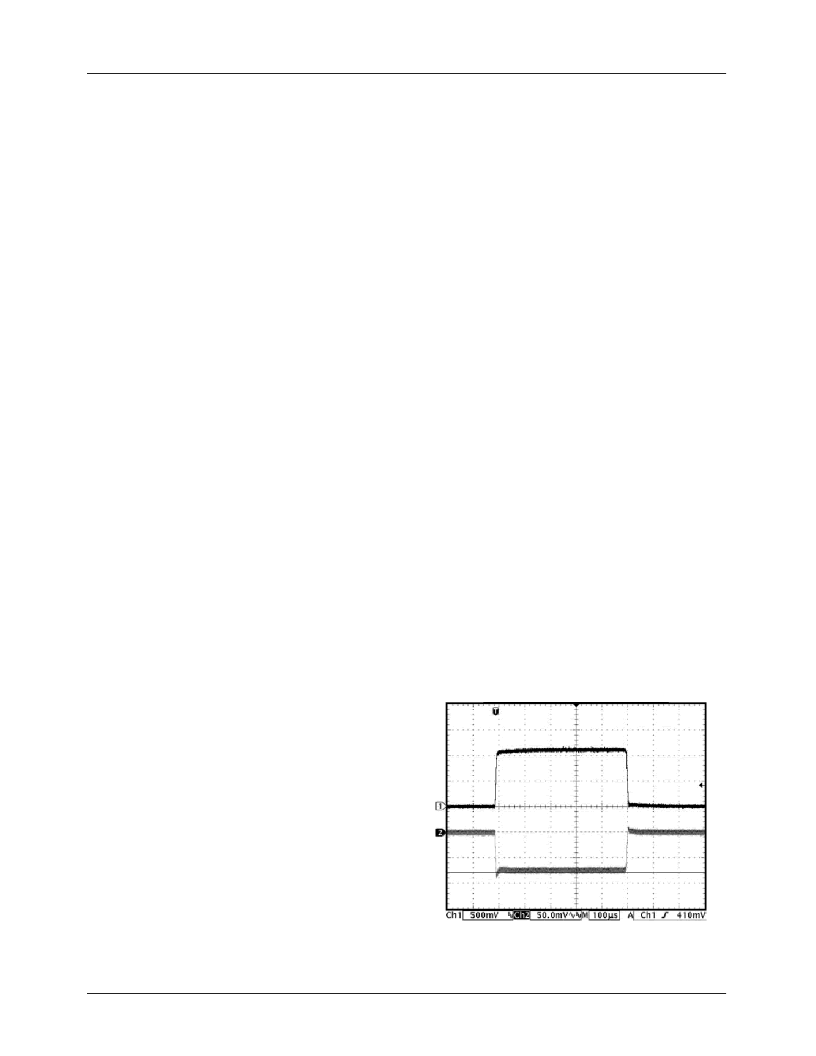
FAN53180
PRODUCT SPECIFICATION
22
REV. 1.0.0 6/10/03
With the multimode feedback structure of the FAN53180,
one needs to set the feedback compensation to make the
converter’s output impedance working in parallel with the
output decoupling meet this goal. There are several poles and
zeros created by the output inductor and decoupling capaci-
tors (output filter) that need to be compensated for.
A type-three compensator on the voltage feedback is
adequate for proper compensation of the output filter. The
expressions given in Equations 25–29 are intended to yield
an optimal starting point for the design; some adjustments
may be necessary to account for PCB and component para-
sitic effects (see the Tuning Procedure for the FAN53180
section).
The first step is to compute the time constants for all of the
poles and zeros in the system:
where, for the FAN53180, R’ is the PCB resistance from the
bulk capacitors to the ceramics and where R
DS
is approxi-
mately the total low-side MOSFET ON resistance per phase
at 25oC. For this example, A
D
is 5, V
RT
equals 0.974V, R’ is
approximately 0.6m
(assuming a 4-layer motherboard) and
L
X
is 375pH for the eight Al-Poly capacitors.
The compensation values can then be solved for using the
following:
Choosing the closest standard values for these components
yields: C
A
= 390pF, R
A
= 16.9k
, C
B
= 1.5nF, and
C
FB
= 33pF.
C
IN
Selection and Input Current di/dt Reduction
In continuous inductor-current mode, the source current of
the high-side MOSFET is approximately a square wave with
a duty ratio equal to n (V
OUT
/V
IN
) and an amplitude of one-
nth of the maximum output current. To prevent large voltage
transients, a low ESR input capacitor sized for the maximum
rms current must be used. The maximum rms capacitor cur-
rent is given by:
Figure 6. Typical Transient Response for Design Example
R
E
n
R
O
A
D
R
DS
+
R
----------------------
V
×
VID
2
--------------------------------------------------------
L
×
1 n
–
(
X
D
×
)
V
RT
×
×
O
VID
+
+
×
×
=
(25)
R
E
3
1.3m
5
5.95m
-------------------------------------------
+
+
×
+
×
=
----------------------------------------–
)
0.974V
1.5V
×
×
55.3m
=
T
A
C
X
R
O
R
'
–
(
)
L
X
R
O
-------
R
-------------------
R
'
–
X
×
+
×
=
(26)
T
A
6.56mF
1.3m
0.6m
–
(
)
------------------
×
+
×
=
--------------------–
4.79
μ
s
=
T
B
R
X
R
'
R
O
–
+
(
)
C
X
×
=
(27)
T
B
1.0m
0.6m
1.3m
–
+
(
)
6.56mF
×
1.97
μ
s
=
=
T
C
V
RT
--------------------------------------------------------
L
A
R
×
------------------------
–
×
VID
E
=
(28)
T
C
0.974V
--------------------------------------------------------------------------------------
650nH
-------------------------------
–
×
6.86
μ
s
=
=
T
D
C
O
C
'
–
C
Z
+
C
X
R
O
------------------------------------------------------------------
=
(29)
T
D
1.3m
220
μ
F
+
(
)
2
×
)
1.3m
×
--------------------------------------------------–
500ns
=
=
C
A
n
------------------------------
R
×
E
T
A
×
B
=
(30)
C
A
----------------------------------------------------
s
253pF
=
=
R
A
T
C
C
A
-------
s
------------------
27.1k
=
=
=
(31)
C
B
T
B
R
B
-------
s
-------------------
1.48nF
=
=
=
(32)
C
FB
T
D
R
A
-------
-------------------
18.5pF
=
=
=
(33)