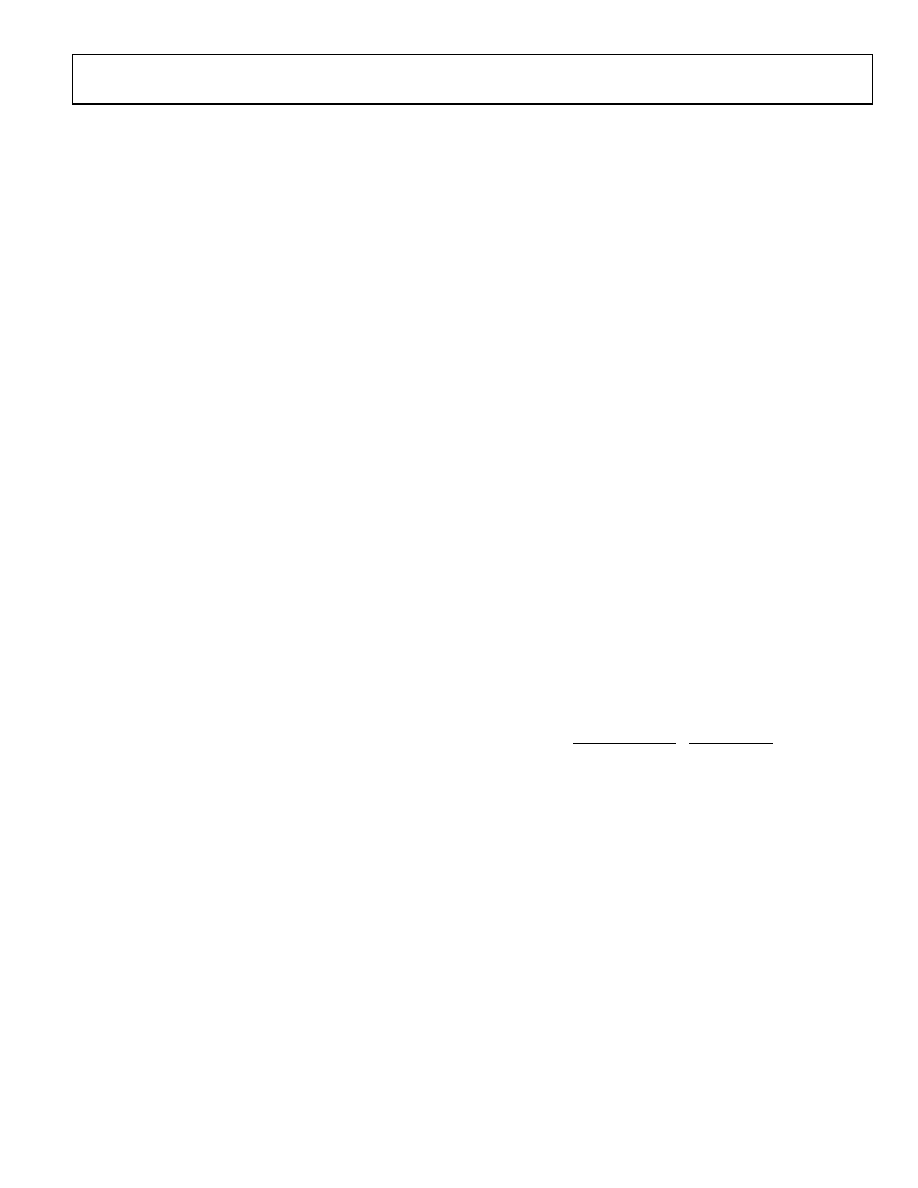
Data Sheet
AD5737
Rev. C | Page 37 of 44
DC-to-DC Converter On-Board Switch
T
he AD5737 contains a 0.425 internal switch. The switch
current is monitored on a pulse-by-pulse basis and is limited
to 0.8 A peak current.
DC-to-DC Converter Switching Frequency and Phase
selected from the dc-to-dc control register (s
ee Table 27). The
phasing of the channels can also be adjusted so that the dc-to-dc
converters can clock on different edges. For typical applications,
a 410 kHz frequency is recommended. At light loads (low output
current and small load resistor), the dc-to-dc converter enters a
pulse-skipping mode to minimize switching power dissipation.
DC-to-DC Converter Inductor Selection
For typical 4 mA to 20 mA applications, a 10 H inductor (such
as the XAL4040-103 from Coilcraft), combined with a switching
frequency of 410 kHz, allows up to 24 mA to be driven into a
load resistance of up to 1 k with an AVCC supply of 4.5 V to
5.5 V. It is important to ensure that the inductor can handle the
peak current without saturating, especially at the maximum
ambient temperature. If the inductor enters saturation mode,
efficiency decreases. The inductance value also drops during
saturation and may result in the dc-to-dc converter circuit not
being able to supply the required output power.
DC-to-DC Converter External Schottky Diode Selection
T
he AD5737 requires an external Schottky diode for correct
operation. Ensure that the Schottky diode is rated to handle the
maximum reverse breakdown voltage expected in operation
and that the maximum junction temperature of the diode is not
exceeded. The average current of the diode is approximately
equal to the ILOAD current. Diodes with larger forward voltage
drops result in a decrease in efficiency.
DC-to-DC Converter Compensation Capacitors
Because the dc-to-dc converter operates in discontinuous conduc-
tion mode, the uncompensated transfer function is essentially a
single-pole transfer function. The pole frequency of the transfer
function is determined by the output capacitance, input and output
voltage, and output load of the dc-to-dc converter. Th
e AD5737uses an external capacitor in conjunction with an internal 150 k
resistor to compensate the regulator loop.
Alternatively, an external compensation resistor can be used in
series with the compensation capacitor by setting the DC-DC
comp bit in the dc-to-dc control register (see
Table 27). In this
case, a resistor of ~50 k is recommended. The advantages of this
Slewing section. For typical applications, a 10 nF dc-to-dc com-
pensation capacitor is recommended.
DC-to-DC Converter Input and Output Capacitor
Selection
The output capacitor affects the ripple voltage of the dc-to-dc
converter and indirectly limits the maximum slew rate at which
the channel output current can rise. The ripple voltage is caused
by a combination of the capacitance and the equivalent series
resistance (ESR) of the capacitor. For typical applications, a
ceramic capacitor of 4.7 F is recommended. Larger capacitors
or parallel capacitors improve the ripple at the expense of
reduced slew rate. Larger capacitors also affect the current
requirements of the AVCC supply while slewing (see the AICC the output of the dc-to-dc converter should be >3 F under all
operating conditions.
The input capacitor provides much of the dynamic current
required for the dc-to-dc converter and should be a low ESR
component. For the
AD5737, a low ESR tantalum or ceramic
capacitor of 10 F is recommended for typical applications.
Ceramic capacitors must be chosen carefully because they can
exhibit a large sensitivity to dc bias voltages and temperature.
X5R or X7R dielectrics are preferred because these capacitors
remain stable over wider operating voltage and temperature
ranges. Care must be taken if selecting a tantalum capacitor to
ensure a low ESR value.
AICC SUPPLY REQUIREMENTS—STATIC
The dc-to-dc converter is designed to supply a VBOOST_x voltage of
VBOOST_x = IOUT × RLOAD + Headroom
(2)
current. Therefore, for a fixed load and output voltage, the
output current of the dc-to-dc converter can be calculated
by the following formula:
CC
V
BOOST
OUT
CC
AV
η
V
I
AV
Efficiency
Out
Power
AI
BOOST
×
=
×
=
(3)
where:
IOUT is the output current from IOUT_x in amperes.
ηV
BOOST
is the efficiency at VBOOST_x as a fraction (see Figure 32