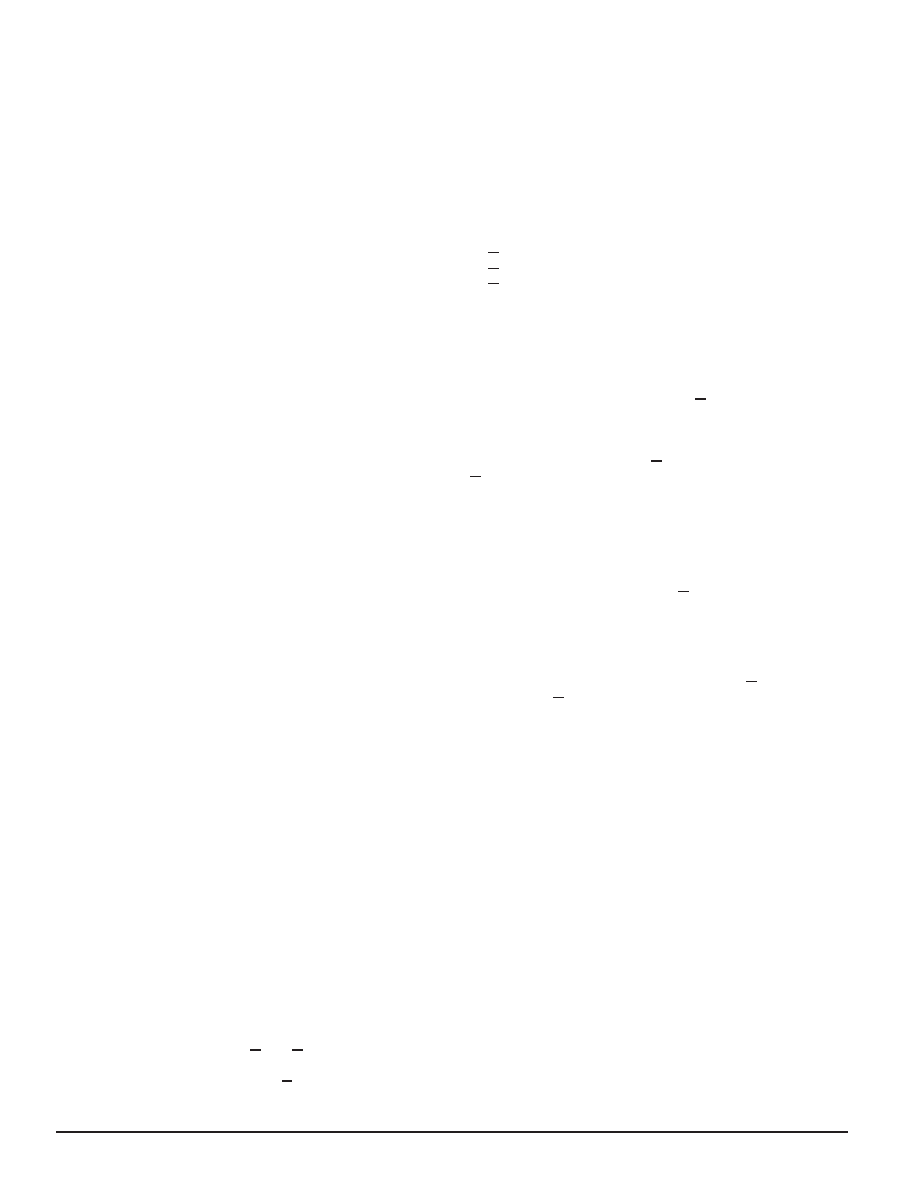
Design Considerations
LCX DATA
BR1339 — REV 3
19
MOTOROLA
Design Considerations
The LCX family was designed to alleviate many of the
drawbacks that are common to current low–voltage logic
circuits. LCX combines the low static power consumption and
the high noise margins of CMOS with a high fan–out, low input
loading and a 50
transmission line drive capability.
Performance features such as 5ns speeds at CMOS power
levels,
±24mA drive, excellent noise, ESD and latch–up
immunity
are
characteristics
that
designers
of
state–of–the–art systems require. LCX provides this level of
performance. To fully utilize the advantages provided by LCX,
the system designer should have an understanding of the
flexibility as well as the trade–offs of CMOS design. The
following section discusses common design concerns relative
to the performance and requirements of LCX.
There are six items of interest which need to be evaluated
when implementing LCX devices in new designs:
Thermal Management — circuit performance and long–
term circuit reliability are affected by die temperature.
Interfacing — interboard and technology interfaces, battery
backup and power down or live insert/extract systems
require some special thought.
Transmission Line Driving — LCX has excellent line driving
capabilities.
Noise effects — As edge rates increase, the probability of
crosstalk and ground bounce problems increases. The
enhanced noise immunity and high threshold levels
improve LCX’s resistance to crosstalk problems.
Board Layout — Prudent board layout will ensure that most
noise effects are minimized.
Power Supplies and Decoupling — Maximize ground and
VCC traces to keep VCC/ground impedance as low as
possible; full ground/VCC planes are best. Decouple any
device driving a transmission line; otherwise add one
capacitor for every package
Thermal Management
Circuit performance and long–term circuit reliability are
affected by die temperature. Normally, both are improved by
keeping the IC junction temperatures low.
Electrical power dissipated in any integrated circuit is a
source of heat. This heat source increases the temperature of
the die relative to some reference point, normally the ambient
temperature of 25
°C in still air. The temperature increase,
then, depends on the amount of power dissipated in the circuit
and on the net thermal resistance between the heat source
and the reference point. See the Thermal Management
Considerations Section on page 283 for LCX power
calculations.
The temperature at the junction is a function of the
packaging and mounting system’s ability to remove heat
generated in the circuit — from the junction region to the
ambient environment. The basic formula for converting power
dissipation to estimated junction temperature is:
TJ = TA + PD(ΘJC + ΘCA)
(1)
or
TJ = TA + PD(ΘJA)
(2)
where
TJ
= maximum junction temperature
TA
= maximum ambient temperature
PD = calculated maximum power dissipation including
effects of external loads (see Power Dissipation in
section III).
ΘJC = average thermal resistance, junction to case
ΘCA = average thermal resistance, case to ambient
ΘJA = average thermal resistance, junction to ambient
This Motorola recommended formula has been approved
by RADC and DESC for calculating a “practical” maximum
operating junction temperature for MIL–M–38510 (JAN)
devices.
Only two terms on the right side of equation (1) can be
varied by the user — the ambient temperature, and the device
case–to–ambient thermal resistance,
ΘCA. (To some extent
the device power dissipation can also be controlled, but under
recommended use the VCC supply and loading dictate a fixed
power dissipation.) Both system air flow and the package
mounting technique affect the
ΘCA thermal resistance term.
ΘJC is essentially independent of air flow and external
mounting method, but is sensitive to package material, die
bonding method, and die area.
For applications where the case is held at essentially a
fixed temperature by mounting on a large or temperature–
controlled heat sink, the estimated junction temperature is
calculated by:
TJ = TC + PD(ΘJC)
(3)
where TC = maximum case temperature and the other
parameters are as previously defined.
Air Flow
The effect of air flow over the packages on
ΘJA (due to a
decrease in
ΘCA) reduces the temperature rise of the
package, therefore permitting a corresponding increase in
power
dissipation
without
exceeding
the
maximum
permissible operating junction temperature.
Even though different device types mounted on a printed
circuit board may each have different power dissipations, all
will have the same input and output levels provided that each
is subject to identical air flow and the same ambient air
temperature. This eases design, since the only change in
levels between devices is due to the increase in ambient
temperatures as the air passes over the devices, or
differences in ambient temperature between two devices.
The majority of users employ some form of air–flow
cooling. As air passes over each device on a printed circuit
board, it absorbs heat from each package. This heat gradient
from the first package to the last package is a function of the
air flow rate and individual package dissipations.
Optimizing The Long Term Reliability of
Plastic Packages
Todays plastic integrated circuit packages are as reliable
as ceramic packages under most environmental conditions.
However when the ultimate in system reliability is required,
thermal management must be considered as a prime system
design goal.