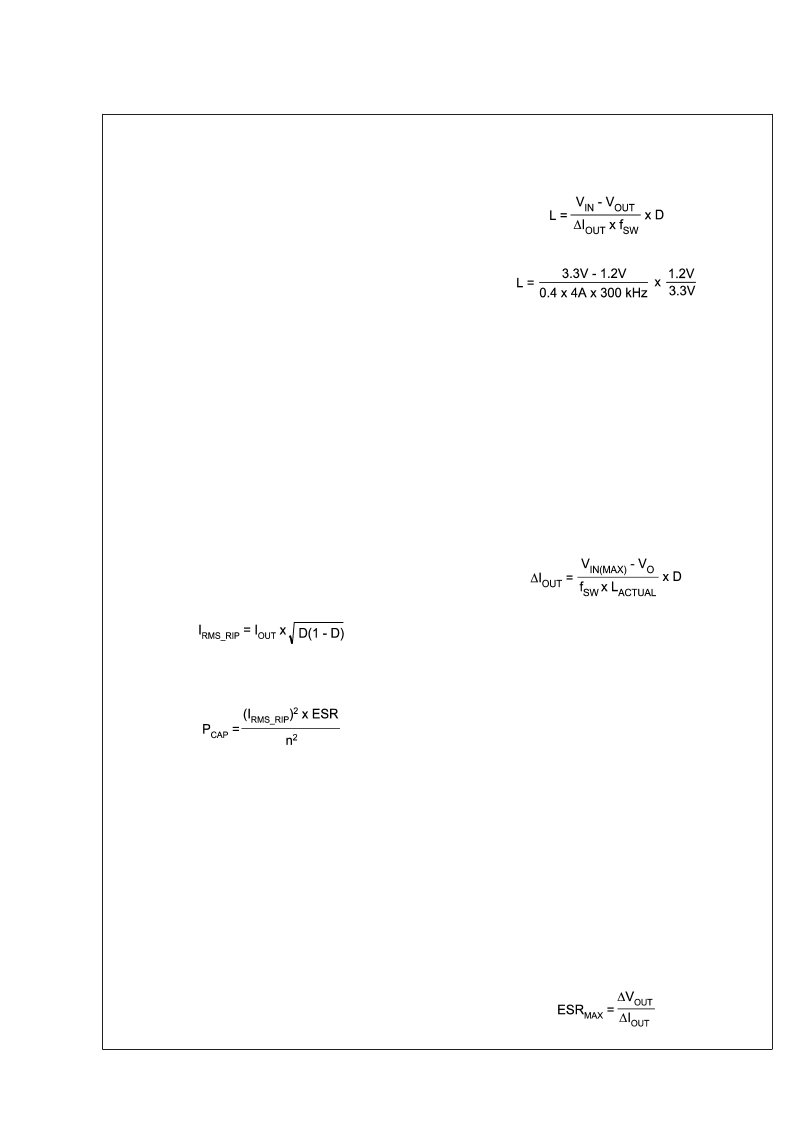
Application Information
(Continued)
will be reduced in turn to a flat level equal to the current limit
threshold. The third benefit of the soft-start capacitor dis-
charge is a smooth, controlled ramp of output voltage when
the current limit condition is cleared.
SHUTDOWN
If the shutdown pin is pulled low, (below 0.8V) the LM2747
enters shutdown mode, and discharges the soft-start capaci-
tor through a MOSFET switch. The high and low-side MOS-
FETs are turned off. The LM2747 remains in this state as
long as V
SD
sees a logic low (see the Electrical Character-
istics table). To assure proper IC start-up the shutdown pin
should not be left floating. For normal operation this pin
should be connected directly to V
CC
or to another voltage
between 1.3V to V
CC
(see the Electrical Characteristics
table).
DESIGN CONSIDERATIONS
The following is a design procedure for all the components
needed to create the Typical Application Circuit shown on
the front page. This design converts 3.3V (V
) to 1.2V
(V
) at a maximum load of 4A with an efficiency of 89%
and a switching frequency of 300 kHz. The same procedures
can be followed to create many other designs with varying
input voltages, output voltages, and load currents.
Input Capacitor
The input capacitors in a Buck converter are subjected to
high stress due to the input current trapezoidal waveform.
Input capacitors are selected for their ripple current capabil-
ity and their ability to withstand the heat generated since that
ripple current passes through their ESR. Input rms ripple
current is approximately:
Where duty cycle D = V
OUT
/V
IN
.
The power dissipated by each input capacitor is:
where n is the number of paralleled capacitors, and ESR is
the equivalent series resistance of each capacitor. The equa-
tion above indicates that power loss in each capacitor de-
creases rapidly as the number of input capacitors increases.
The worst-case ripple for a Buck converter occurs during full
load and when the duty cycle (D) is 0.5. For this 3.3V to 1.2V
design the duty cycle is 0.364. For a 4A maximum load the
ripple current is 1.92A.
Output Inductor
The output inductor forms the first half of the power stage in
a Buck converter. It is responsible for smoothing the square
wave created by the switching action and for controlling the
output current ripple (
I
OUT
). The inductance is chosen by
selecting between tradeoffs in efficiency and response time.
The smaller the output inductor, the more quickly the con-
verter can respond to transients in the load current. How-
ever, as shown in the efficiency calculations, a smaller in-
ductor requires a higher switching frequency to maintain the
same level of output current ripple. An increase in frequency
can mean increasing loss in the MOSFETs due to the charg-
ing and discharging of the gates. Generally the switching
frequency is chosen so that conduction loss outweighs
switching loss. The equation for output inductor selection is:
L = 1.6 μH
Here we have plugged in the values for output current ripple,
input voltage, output voltage, switching frequency, and as-
sumed a 40% peak-to-peak output current ripple. This yields
an inductance of 1.6 μH. The output inductor must be rated
to handle the peak current (also equal to the peak switch
current), which is (I
OUT
+ (0.5 x
I
OUT
)) = 4.8A, for a 4A
design.
The Coilcraft DO3316P-222P is 2.2 μH, is rated to 7.4A
peak, and has a direct current resistance (DCR) of 12 m
.
After selecting the Coilcraft DO3316P-222P for the output
inductor, actual inductor current ripple should be re-
calculated with the selected inductance value, as this infor-
mation is needed to select the output capacitor. Re-
arranging the equation used to select inductance yields the
following:
V
IN(MAX)
is assumed to be 10% above the steady state input
voltage, or 3.6V at V
= 3.3V. The re-calculated current
ripple will then be 1.2A. This gives a peak inductor/switch
current will be 4.6A.
Output Capacitor
The output capacitor forms the second half of the power
stage of a Buck switching converter. It is used to control the
output voltage ripple (
V
OUT
) and to supply load current
during fast load transients.
In this example the output current is 4A and the expected
type of capacitor is an aluminum electrolytic, as with the
input capacitors. Other possibilities include ceramic, tanta-
lum, and solid electrolyte capacitors, however the ceramic
type often do not have the large capacitance needed to
supply current for load transients, and tantalums tend to be
more expensive than aluminum electrolytic. Aluminum ca-
pacitors tend to have very high capacitance and fairly low
ESR, meaning that the ESR zero, which affects system
stability, will be much lower than the switching frequency.
The large capacitance means that at the switching fre-
quency, the ESR is dominant, hence the type and number of
output capacitors is selected on the basis of ESR. One
simple formula to find the maximum ESR based on the
desired output voltage ripple,
V
OUT
and the designed out-
put current ripple,
I
OUT
, is:
L
www.national.com
14