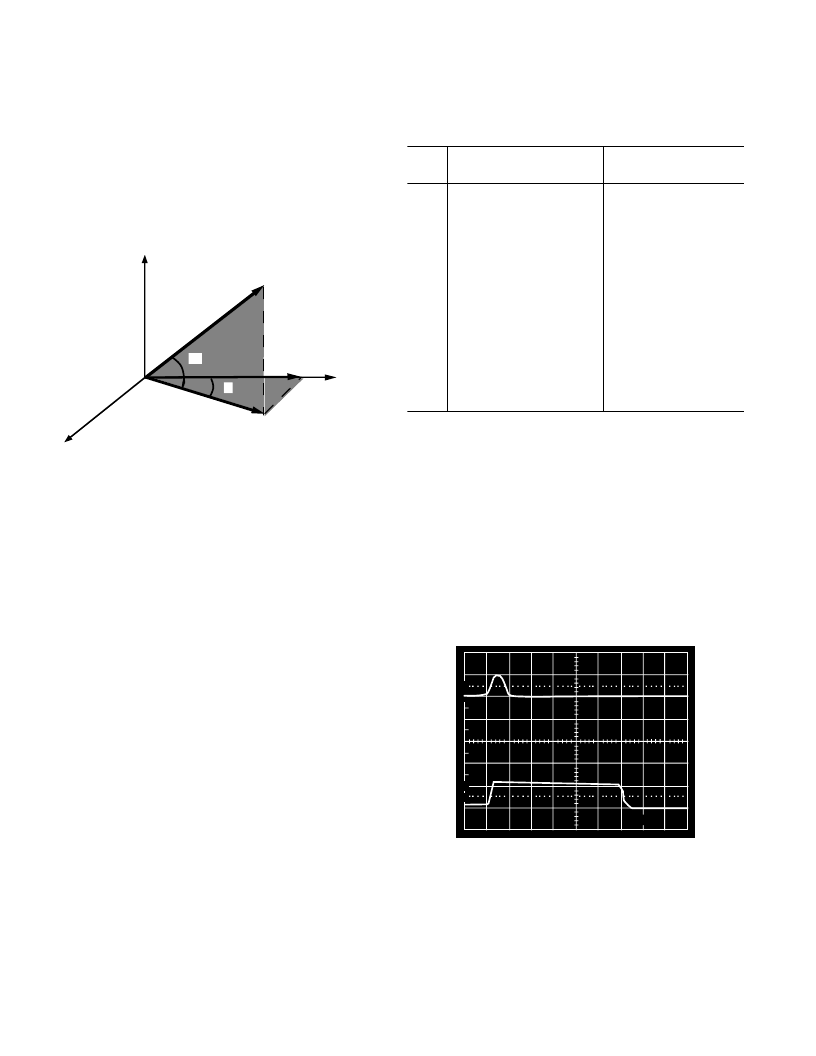
ADXL05
REV. B
–6–
package. Figure 2c describes a three dimensional acceleration
vector (A
X YZ
) which might act on the sensor, where A
X
is the
component of interest. T o determine A
X
, first, the component
of acceleration in the X Y plane (A
X Y
) is found using the cosine
law:
A
X Y
=
A
X YZ
(
cos
θ
X Y
)
then
A
X
=
A
X Y
(
cos
θ
X
)
Therefore: Nominal V
PR
=
200
mV
/
g
(
A
X YZ
)
(cos
θ
X Y
) cos
θ
X
Axyz
–Z AXIS
X AXIS
Y AXIS
Axy
Ax
θ
xy
θ
x
Figure 2c. A Vector Analysis of an Acceleration Acting
Upon the ADXL05 in Three Dimensions
Note that an ideal sensor will react to forces along or at angles
to its sensitive axis but will reject signals from its various trans-
verse axes, i.e., those exactly 90
°
from the sensitive “X ” axis.
But even an ideal sensor will produce output signals if the trans-
verse signals are not exactly 90
°
to the sensitive axis. An accel-
eration that is acting on the sensor from a direction different
from the sensitive axis will show up at the ADX L05 output at a
reduced amplitude.
T able I shows the percentage signals resulting from various
θ
X
angles. Note that small errors in alignment have a negligible
effect on the output signal. A 1
°
error will only cause a 0.02%
error in the signal. Note, however, that a signal coming 1
°
off of
the transverse axis (i.e., 89
°
off the sensitive axis) will still con-
tribute 1.7% of its signal to the output. T hus large transverse
signals could cause output signals as large as the signals of
interest. T able I may also be used to approximate the effect of
the ADX L05’s internal errors due to misalignment of the die to
the package. For example: a 1 degree sensor alignment error will
allow 1.7% of a transverse signal to appear at the output.
T able I. Ideal Output Signals for Off Axis Applied
Accelerations Disregarding Device Alignment and
T ransverse Sensitivity E rrors
% of Signal Appearing
at Output
Output in
g
s for a 5
g
Applied Acceleration
θ
X
0
1
°
2
°
3
°
5
°
10
°
30
°
45
°
60
°
80
°
85
°
87
°
88
°
89
°
90
°
100%
99.98%
99.94%
99.86%
99.62%
98.48%
86.60%
70.71%
50.00%
17.36%
8.72%
5.25%
3.49%
1.7%
0%
5.000 (On Axis)
4.999
4.997
4.993
4.981
4.924
4.330
3.536
2.500
0.868
0.436
0.263
0.175
0.085
0.000 (T ransverse Axis)
Mounting Fixture Resonances
A common source of error in acceleration sensing is resonance
of the mounting fixture. For example, the circuit board that the
ADX L05 mounts to may have resonant frequencies in the same
range as the signals of interest. T his could cause the signals
measured to be larger than they really are. A common solution
to this problem is to dampen these resonances by mounting the
ADX L05 near a mounting post or by adding extra screws to
hold the board more securely in place.
When testing the accelerometer in your end application, it is
recommended that you test the application at a variety of fre-
quencies in order to ensure that no major resonance problems
exist (refer to Analog Devices Application Note AN-379).
10
90
100
0%
0.5ms
Figure 3. 500 g Shock Overload Recovery. Top Trace, PCB
Reference Accelerometer Output: 500 g/Vertical Division.
Bottom Trace, ADXL05 Output at V
PR