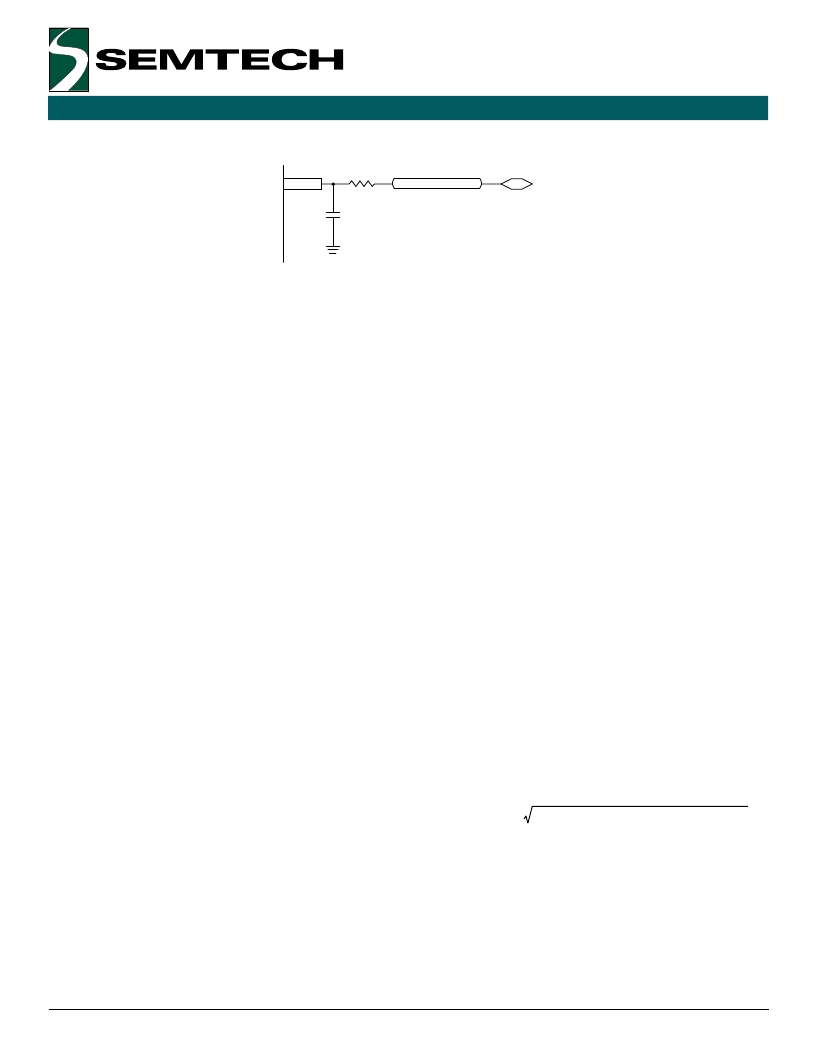
5
TEST AND MEASUREMENT PRODUCTS
www.semtech.com
PE-A2
Optimizing the Output Configuration of
Semtech Bipolar Pin Drivers
Revision 1 / December 18, 2002
Figure 6. External Components for Obtaining Optimum Impedance Matching
to a Transmission Line with only the Driver Connected
46.5
DUT Pin
DOUT
50
Transmission Line
0805
DCL Part
~ 3pF
Component Placement
Waveform distortion also occurs if the signal travels too
far through the external components and traces before
being injected into the transmission line, so these external
components should be placed as close to the part as
possible and the connecting traces should be as short as
possible. Since Semtech EVM boards were designed to
allow a socket to be used for testing parts, the external
components are not always placed as close to the socket
as would be possible otherwise. It is recommended that
the external resistors and inductors be moved as close as
possible to the corresponding DCL pins to minimize the
time delay/reflection distortions.
Placement of the external components can also be
improved by using smaller components or smaller pad
sizes. For instance, 0603 size inductors are used on
Semtech EVM boards in order to make switching
components when finding optimum inductor values easier
In a production system where board space is at a premium,
0402 or smaller inductors may be used. Since the external
impedance-matching resistors may have to dissipate a
significant amount of power the size of these components
cannot usually be reduced significantly. However it may
be possible to reduce the size of the pads beneath these
components since boards in ATE systems do not experience
the temperature and mechanical stress many other boards
experience. For instance, 0805 components can often
be installed on 0603 pad sizes, reducing the amount of
board space required. The reliability expert at the board
assembly house used should be consulted for determining
the amount of pad size reduction that can be used in a
particular case.
Effect of DUT Capacitance
The DUT pin often has a parasitic capacitance associated
with it which slows down the rise/fall times of the incoming
signal. Since this capacitance is usually at the
unterminated end of the transmission line, inductor
compensation, as described previously, is not useful.
Adding an inductor in series at this point will actually
increase the amount of waveform distortion rather than
decrease it, so this approach is not recommended in this
situation. (If the transmission line continues on past the
DUT, such as in a fly-by test situation, then using an
inductor for compensation can be useful).
When the DUT is at the end of the transmission line, the
rise/fall time at the DUT pin is the rise/fall time of the
driver in combination with the rise fall time due to the
R-C time constant of the 50 ohm transmission line and
the parasitic capacitance. Since one R-C time constant
is equal to the voltage changing a factor of (1 - 1/e) or
63.2% of the way to the final value, the 10% to 90%
transition time is 2.20 times the R-C time constant and
the 20% to 80% transition time is 1.39 times the R-C
time constant. The transition time at the DUT pin is then:
DUT r/f time = (Driver r/f time)
2
+ (R–C r/f time)
2