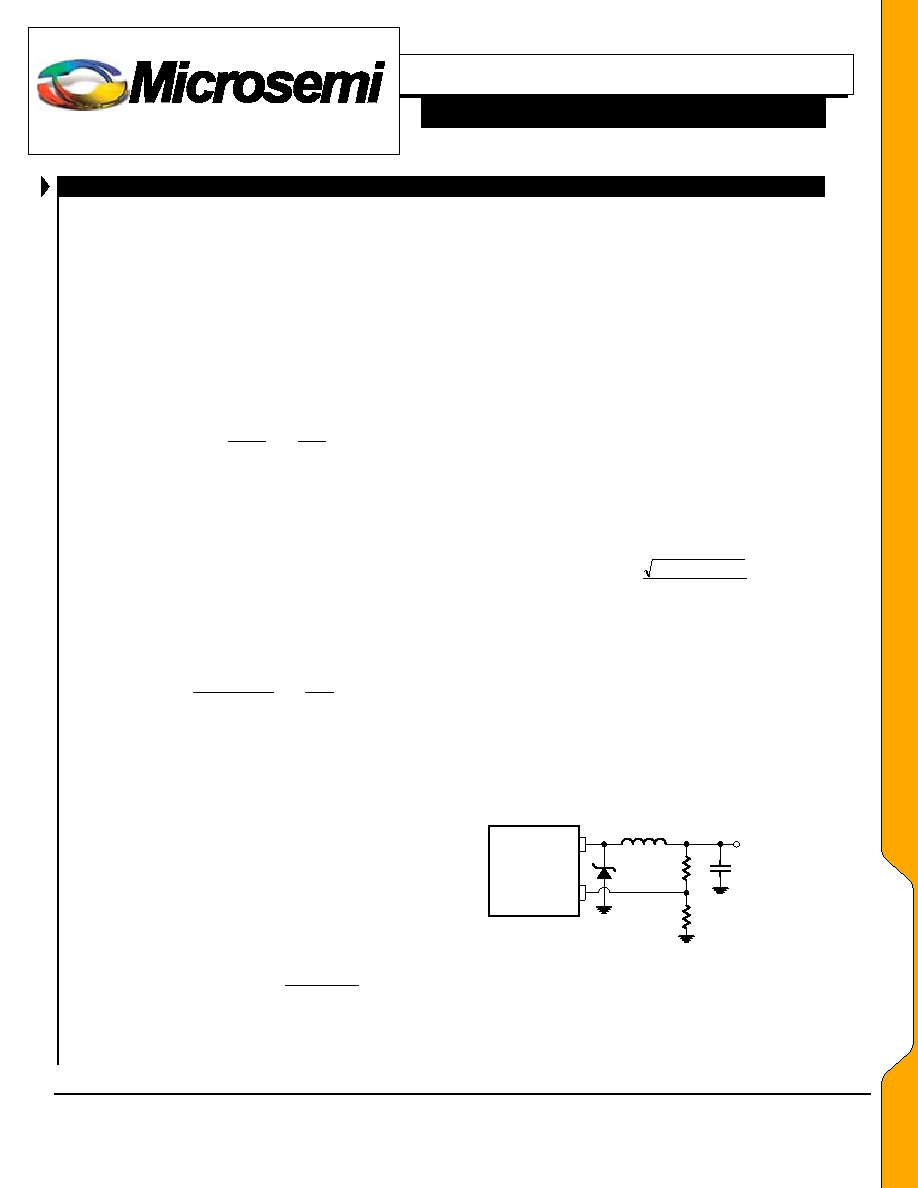
LX1910
PRELIMINARY DATA SHEET
Microsemi
Integrated Products Division
11861 Western Avenue, Garden Grove, CA. 92841, 714-898-8121, Fax: 714-893-2570
Page 6
WWW
.Microse
m
i
.CO
M
High Frequency Step Down Regulator
I N T E GR A T ED
PRODUCT S
Copyright
2000
Rev. 0.9a, 2004-04-16
APPLICATION NOTE
The typical LX1910 application circuit is depicted in
figure 2. Component selection is dependant on the required
load, and begins with the selection of an output inductor.
INDUCTOR SELECTION
Generally the output inductance value will be from 1
H
to 4.7
H. The inductor value is sized to meet the desired
inductor ripple current. While smaller values of inductance
will increase the transient response capability of the
regulator, they will also raise the inductor ripple current
causing an increase in output ripple voltage.
This
relationship is given by the following equation:
=
IN
OUT
OSC
RIPPLE
V
1
L
f
1
I
eq. 1
where VIN is the maximum input voltage for the
application, fOSC is the minimum oscillator frequency, and
VOUT is the output voltage. Choosing these conditions will
ensure that the calculated inductance value will correspond
to the worst case inductor ripple current.
Generally, it is accepted practice to begin by selecting an
inductor based on an inductor ripple current which is 20%
to 40% of the maximum DC load current (IDC).
Substituting this value and solving eq. 1 for the inductor
value yields:
()
=
IN
OUT
DC
OSC
V
1
%
20
I
f
1
L
eq. 2
The DC rating of the inductor needs to be equivalent to
the maximum DC current of the application plus half of the
inductor ripple current.
Generally, better efficiency is obtained when the
inductor ripple current is minimized.
In addition, the
inductor DC resistance (DCR) also plays a significant role.
OUTPUT CAPACITOR SELECTION
The selection of output capacitor is generally driven by
the required output ripple voltage which is largely
controlled by the capacitive effective series resistance
(ESR). The output ripple voltage is given by:
+
=
OUT
OSC
RIPPLE
C
f
8
1
ESR
I
V
eq. 3
where COUT is the total output capacitance. Low ESR
values not only yield lower output ripple voltages, but also
improve the transient response of the circuit.
Knowing the desired output ripple voltage, a capacitor
type can then be selected. Using eq. 3 it can then be
determined how many of the chosen capacitor type will
need to be used in the application circuit.
Once the desired ripple voltage is met, the RMS current
rating of the capacitors can be assessed from capacitor’s
manufacturer datasheet to ensure it is not exceeded.
Generally, once the ESR requirement has been met the
RMS current rating requirement has been more than
satisfied.
INPUT CAPACITOR SELECTION
In PWM operation the source current of the internal
MOSFET, at the SW pin, is a square wave at a duty cycle
of VOUT/VIN. Localized low ESR decoupling must be
placed at the pin in order to prevent large voltage
transients. The input capacitors are selected according to
their maximum RMS current rating which is given by:
()
IN
OUT
IN
OUT
)
MAX
(
OUT
)
RMS
(
SW
V
I
=
eq. 4
where IOUT(MAX) is the maximum application DC output
current and VIN is the maximum input voltage. Once a
capacitor is selected, the number of capacitors needed can
be determined using the capacitor manufacturer’s RMS
current rating ensuring that it exceeds the calculated RMS
switch current.
OUTPUT VOLTAGE PROGRAMMING
The output voltage, for the LX1910, is adjustable and
set using a resistor divider to sense the output voltage as
shown in Figure 4.
V
OUT
LX1910
FB
SW
R
1
R
2
4.7
H
Figure 4 –
Output Voltage Programming
The output voltage is determined using the following
relationship:
AA
PP
LL
IICC
AA
TT
IIOO
NN
SS