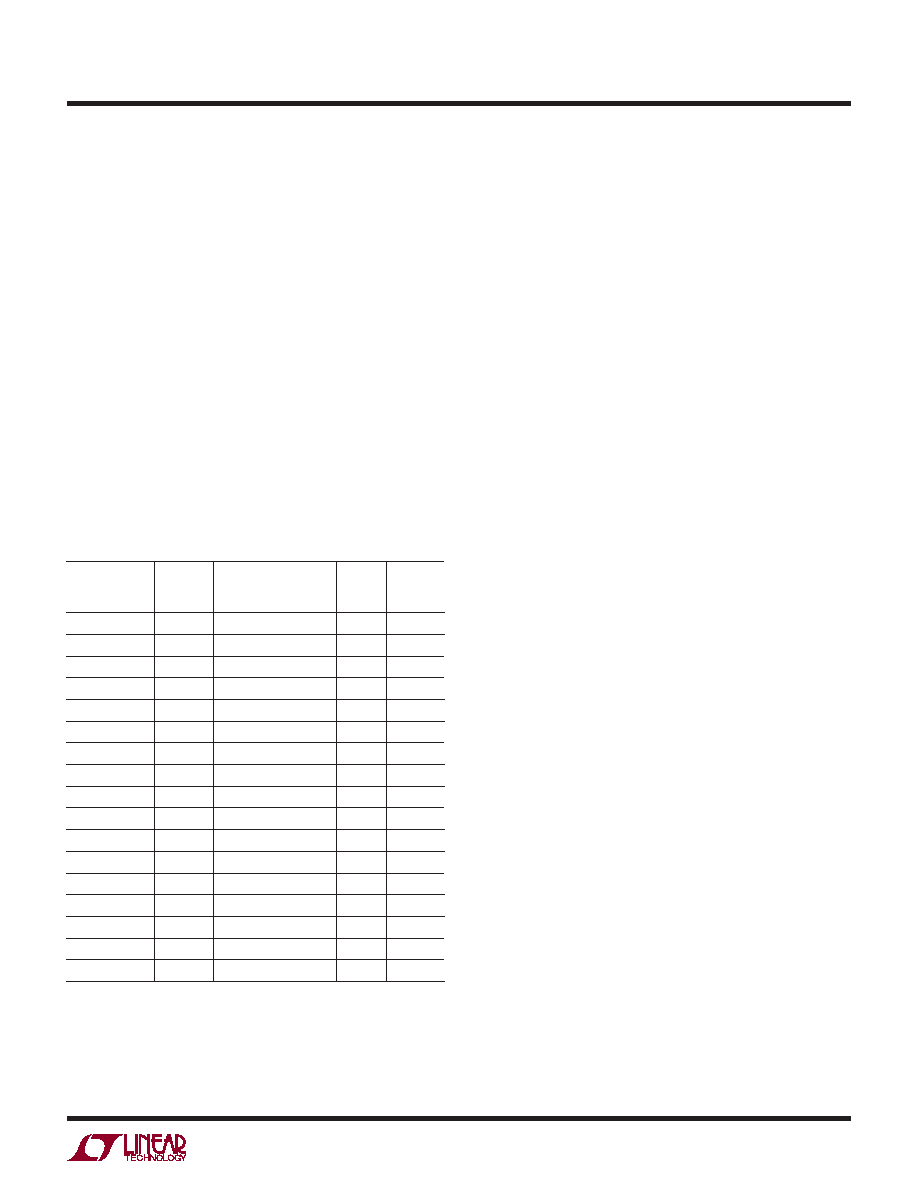
LTM8062/LTM8062A
11
8062fa
APPLICATIONS INFORMATION
VIN Input Supply
The LTM8062/LTM8062A are biased directly from the
charger input supply through the VIN pin. This pin pro-
vides large switched currents, so a high quality low ESR
decoupling capacitor is recommended to minimize volt-
age glitches on VIN. 4.7μF is typically adequate for most
charger applications.
Reverse Protection Diode
The LTM8062/LTM8062A integrate a high voltage power
Schottky diode to provide input reverse voltage protec-
tion. The anode of this diode is connected to VINA, and
the cathode is connected to VIN. There is a small amount
of capacitance at each end; please see the Block Diagram.
The integrated diode can also be used to block battery
discharge leakage paths. The LTM8062/LTM8062A switch
and drive circuitry are designed to stand off some reverse
voltage from BAT to VIN, but leakage paths exist that can
put a small load on the battery if VIN falls below BAT.
Specifically, the RUN pin has a small bias current and
there is a 100k resistor tied to VINREG to GND. If either
of these pins is connected to VIN when it is below BAT,
it can present a small but finite discharge current to the
battery. This discharge current may be blocked by the
integrated Schottky diode if the RUN and VINREG circuits
are tied to VINA.
Input Supply Voltage Regulation
The LTM8062/LTM8062A contain a voltage monitor pin
that enables programming a minimum operational volt-
age. There is a 1% 100k resistor from VINREG to GND.
Connecting a resistor from VIN to the VINREG pin enables
programming of minimum input supply voltage, typically
used to program the peak power voltage for a solar panel.
Maximum charge current is reduced when the VINREG pin
is below the regulation threshold of 2.7V.
If the VINREG function is not used, and if the input supply
cannot provide enough power to satisfy the requirements
ofanLTM8062/LTM8062Acharger,theinputsupplyvoltage
For most applications, the design process is straight
forward, summarized as follows:
1. Look at Table 1 and find the row that has the desired
input voltage range and battery float voltage.
2. Apply the recommended CIN and RADJ values.
3. Connect BIAS as indicated.
While these component combinations have been tested
for proper operation, it is incumbent upon the user to
verify proper operation over the intended system’s line,
load and environmental conditions. Bear in mind that the
maximum output current is limited by junction tempera-
ture, the relationship between the input and output voltage
magnitude and polarity and other factors. Please refer to
the graphs in the Typical Performance Characteristics
section for guidance.
Table 1. Recommended Component Values and Configuration
(TA = 25°C)
VIN RANGE (V)* VBAT (V)
CIN
RADJ1
TOP
(k)
RADJ2
BOTTOM
(k)
6 to 32
3.6
4.7F 1206 X7R 50V
274
2870
6 to 32
4.1
4.7F 1206 X7R 50V
312
1260
6 to 32
4.2
4.7F 1206 X7R 50V
320
1150
6.25 to 32
4.7
4.7F 1206 X7R 50V
357
835
9.5 to 32
7.05
4.7F 1206 X7R 50V
530
464
9.75 to 32
7.2
4.7F 1206 X7R 50V
549
459
11 to 32
8.2
4.7F 1206 X7R 50V
626
417
11.5 to 32
8.4
4.7F 1206 X7R 50V
642
412
12.75 to 32
9.4
4.7F 1206 X7R 50V
715
383
16.5 to 32
12.3
4.7F 1206 X7R 50V
942
344
17 to 32
12.6
4.7F 1206 X7R 50V
965
340
18.25 to 32
13.5
4.7F 1206 X7R 50V
1020
328
19 to 32
14.08
4.7F 1206 X7R 50V
1090
332
19.5 to 32
14.42
4.7F 1206 X7R 50V
1110
328
23 to 32
16.4
4.7F 1206 X7R 50V
1240
312
23.5 to 32
16.8
4.7F 1206 X7R 50V
1270
309
26 to 32
18.8
4.7F 1206 X7R 50V
1420
301
*Operating range, VIN must be 3.3V above VBAT to start. Input bulk
capacitance is required.