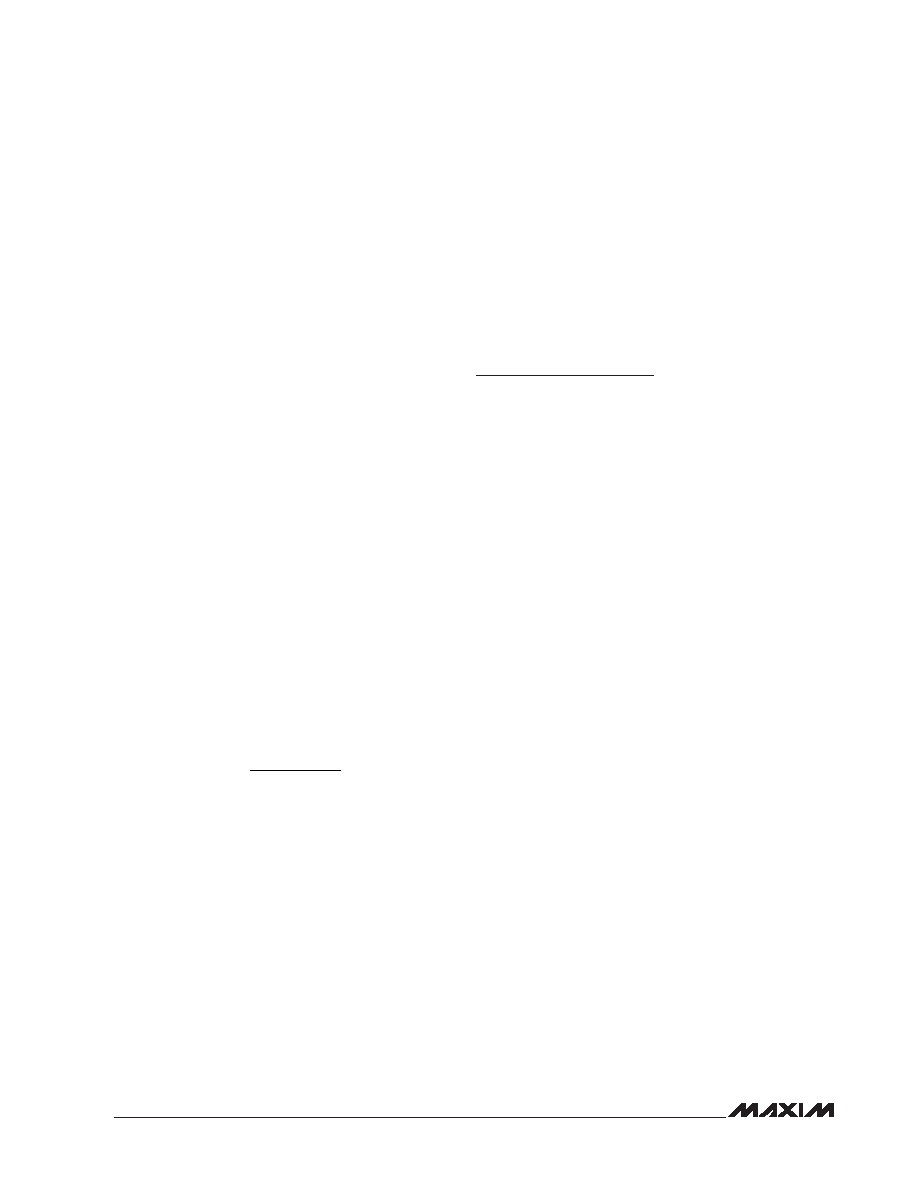
MAX17129/MAX17149
Low-Cost, 6-String WLED Drivers with
Quick-PWM Step-Up Converter
16
Current-Source Fault Protection
An LED fault open/short is detected after the startup.
When one or more strings fail after the startup, the corre-
sponding current source is disabled. The remaining LED
strings still operate normally.
LED Short and String Mismatch Protection
The devices can tolerate a slight mismatch between LED
strings. When severe mismatches or WLED shorts occur,
the FB_ voltages are uneven because of mismatched
voltage drop across strings. When FB_ voltage is higher
than 8V (typ) after LED turn on, an LED short is detected.
The remaining LED strings can still operate normally.
Open Current-Source Protection
The devices’ step-up regulator output voltage is regu-
lated according to the minimum FB_ voltages on all
the strings in use. If one or more strings are open, the
respective FB_ pins are pulled to ground. For any FB_
lower than 700mV (max), the corresponding current
source is disabled. The remaining LED strings can
still operate normally. If all strings in use are open, the
devices shut the step-up regulator down.
PWM Dimming Control
The devices perform brightness control with the BRT
input signal. The current in the LEDs follows the duty
cycle and frequency of the BRT signal. The dimming
frequency can be from 0.1kHz to 25kHz.
Full-Scale LED Current
The full-scale LED current ILED_FS is set by the resistor
connected from ISET to GND and:
LED_FS
ISET
20mA 100k
I
R
×
=
The acceptable resistance range for ISET is 44.44kI <
RISET < 200kI, which corresponds to a full-scale LED
current of 45mA > ILED_FS > 10mA.
Hybrid Dimming Mode
The devices can implement hybrid dimming by control-
ling the voltage on the EN pin (between 1.4V and 1.8V)
after the device is enabled. In hybrid dimming mode,
the LED current is 25% of the full-scale current set by
the resistor on the ISET pin. The purpose of this hybrid
dimming operation is to improve system efficiency by
reducing the current in the LEDs, therefore reducing the
forward drop in them.
Thermal Shutdown
The devices include a thermal-protection circuit. When
the junction temperature exceeds TJ = +160NC (typ), a
thermal sensor immediately activates the fault protection,
which shuts down the step-up regulator and all current
sources, allowing the devices to cool down. Once the
devices cool down by approximately 15NC, the ICs start
up automatically. The thermal-overload protection pro-
tects the devices in the event of fault conditions. For con-
tinuous operation, do not exceed the absolute maximum
junction temperature rating of TJ = +150NC.
Design Procedure
All the devices’ designs should be prototyped and tested
prior to production.
External component value choice is primarily dictated
by the output voltage and the maximum load current, as
well as maximum and minimum input voltages. Begin by
selecting an inductor value. Once the inductor is known,
choose the diode and capacitors.
Inductor Selection
The inductance, peak current rating, series resistance,
and physical size should all be considered when select-
ing an inductor. These factors affect the converter’s oper-
ating mode, efficiency, maximum output load capability,
transient response time, output voltage ripple, and cost.
The maximum output current, input voltage, output
voltage, and switching frequency determine the induc-
tor value. Very high inductance minimizes the current
ripple, and therefore reduces the peak current, which
decreases core losses in the inductor and I2R losses in
the entire power path. However, large inductor values
also require more energy storage and more turns of wire,
which increase physical size and I2R copper losses. Low
inductor values decrease the physical size but increase
the current ripple and peak current. Finding the best
inductor involves the compromises among circuit effi-
ciency, inductor size, and cost.
In choosing an inductor, the first step is to determine the
operating mode: continuous-conduction mode (CCM)
or discontinuous-conduction mode (DCM). When CCM
mode is chosen, the ripple current and the peak current
of the inductor can be minimized. If a small-size inductor
is required, DCM mode can be chosen. In DCM mode,
the inductor value and size can be minimized but the
inductor ripple current and peak current are higher than
those in CCM. The controller can be stable, but there is a
maximum inductor value requirement to ensure the DCM
operating mode. The equations used here include a con-
stant LIR, which is the ratio of the inductor peak-to-peak
ripple current to the average DC inductor current at the
full-load current. The controller operates in DCM mode