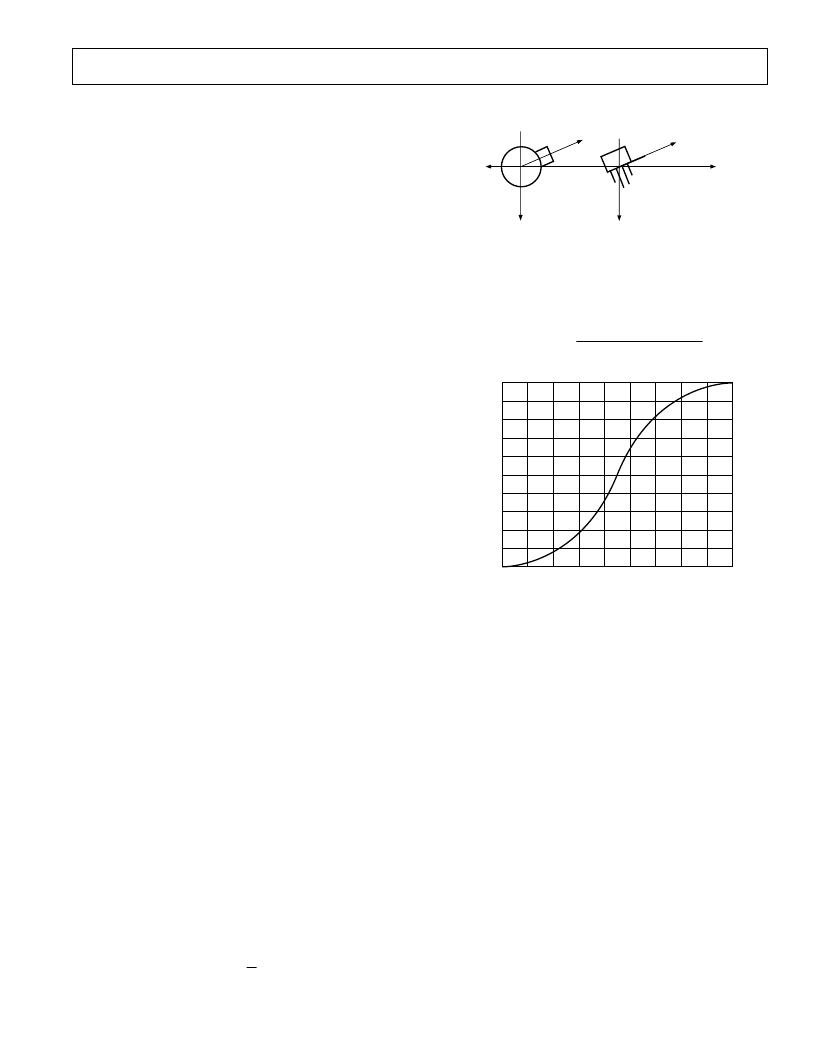
ADXL05
–15–
REV. B
Additional Noise Reduction T echniques
Shielded wire should be used for connecting the accelerometer to
any circuitry that is more than a few inches away—to avoid 60 Hz
pickup from ac line voltage. Ground the cable’s shield at only one
end and connect a separate common lead between the circuits;
this will help to prevent ground loops. Also, if the accelerometer
is inside a metal enclosure, this should be grounded as well.
Methods for Reducing 0
g
Offset Drift
When using any accelerometer with a dc (gravity sensing) re-
sponse, the 0
g
offset level will exhibit some temperature drift.
For very high accuracy applications, one very straightforward
approach is to use a low cost crystal oven to maintain the accel-
erometer at a constant temperature. T hese ovens are available in
a variety of different temperatures. After the circuit has been built
and is operating correctly, the crystal oven can be mounted over
the accelerometer and powered off the same +5 V power supply.
T he ovens may be purchased from Isotemp Research, Inc., P.O.
Box 3389, Charlottesville, VA 22903, phone 804-295-3101. For
more details on crystal oven compensation, refer to application
note AN-385.
Other methods for 0
g
drift compensation include using a low
cost temperature sensor such as the AD22100 to supply a mi-
croprocessor with the device temperature. If the drift curve of
the accelerometer is stored in the
μ
P, then a software program
can be used to subtract out the drift. Alternatively, a simple 1st
order (straight line) correction circuit can be used to subtract
out the linear portion of the accelerometer’s drift by using a
temperature sensor and op amp to supply a small compensation
current. For more details on software and hardware drift com-
pensation, refer to application note AN-380.
ACCE LE ROME T E R APPLICAT IONS
Popular applications for low
g
accelerometers tend to fall into
three categories: measurement of tilt and orientation, inertial
measurement of acceleration, velocity and distance, and vibra-
tion or shock measurement.
T he ADX L05 is a “dc” accelerometer, meaning that it is ca-
pable of measuring static accelerations such as the Earth’s grav-
ity. T he ADX L05 differs from other acceleration measurement
technologies such as piezoelectric and piezofilm sensors which
can only respond to ac signals greater than approximately 1 Hz.
T his dc capability is required for tilt and inertial measurement.
For ac shock or vibration the ADX L05 can measure frequencies
of up to 4 kHz and has the added benefit of measuring all the
way down to dc.
Using the ADX L05 in T ilt Applications
T he ADX L05’s precision dc characteristics make it suitable for
tilt measurement. It can directly measure the Earth’s gravity and
use this constant force as a position reference to determine incli-
nation. As shown in Figure 28, the accelerometer should be
mounted so that its sensitive axis is perpendicular to the force of
gravity, i.e., parallel to the Earth’s surface. In this manner, it
will be most sensitive to changes in orientation (when it is orien-
tated 90
°
to the force of gravity). Its output can be then de-
scribed by the sine function; a tilt occurring at an angle
θ
will
cause a voltage output equal to:
V
OUT
=
Accelerometer ScaleFactor
V
g
×
sin
θ
( )
×
1
g
+
zerogoutput
(
V
)
θ
1g
1g
θ
Figure 28. Two Possible Orientations for Tilt Measurement
Conversely, for a given acceleration signal and assuming no
other changes in the axis or interfering signals, the tilt angle is
proportional to the voltage output as shown in Figure 29. T he
angle,
θ
can be calculated using:
θ
=
arcsin 1
g
×
V
OUT
±
zerogoutput
(
V
)
ScaleFactor
(
V
/
g
)
ANGLE OF TILT
500
400
–500
–90
90
–70
–50
–30
–10
100
–200
–300
–400
300
200
–100
0
10
30
50
70
V
O
Figure 29. V
OUT
vs. Tilt Angle
T he use of an accelerometer in tilt applications has several ad-
vantages over the use of a traditional tilt sensor. A traditional tilt
sensor consists of glass vial filled with a conductive liquid, typi-
cally a mercury or electrolytic solution. Besides being larger
than an X L05, it requires additional signal conditioning cir-
cuitry. T he settling time and frequency response is limited by
the amount of time required for the liquid to stop sloshing
around in the vial. In high vibration environments, or where
high lateral accelerations may be present, it may not be possible
to resolve the tilt signal above the “slosh” noise. T he acceler-
ometer has faster frequency (up to 50
×
) response and set-
tling time. Interfering vibrations may be filtered out if
necessary, an impossibility with a liquid tilt sensor, since one
cannot filter the liquid. Finally, in the presence of lateral accel-
erations, an accelerometer provides more useful information,
i.e., an acceleration signal, which if cleverly signal processed,
can provide both a tilt and an acceleration output. A single ac-
celerometer can be used to measure tilt over a 180
°
range; two
accelerometers gives a complete 360
°
of measurement.
An important characteristic for an accelerometer used in a tilt
application is its 0
g
offset stability over temperature. T he
ADX L05 typically exhibits offsets that deviate no more than
0.1
g
over the 0
°
C to +70
°
C temperature range, corresponding