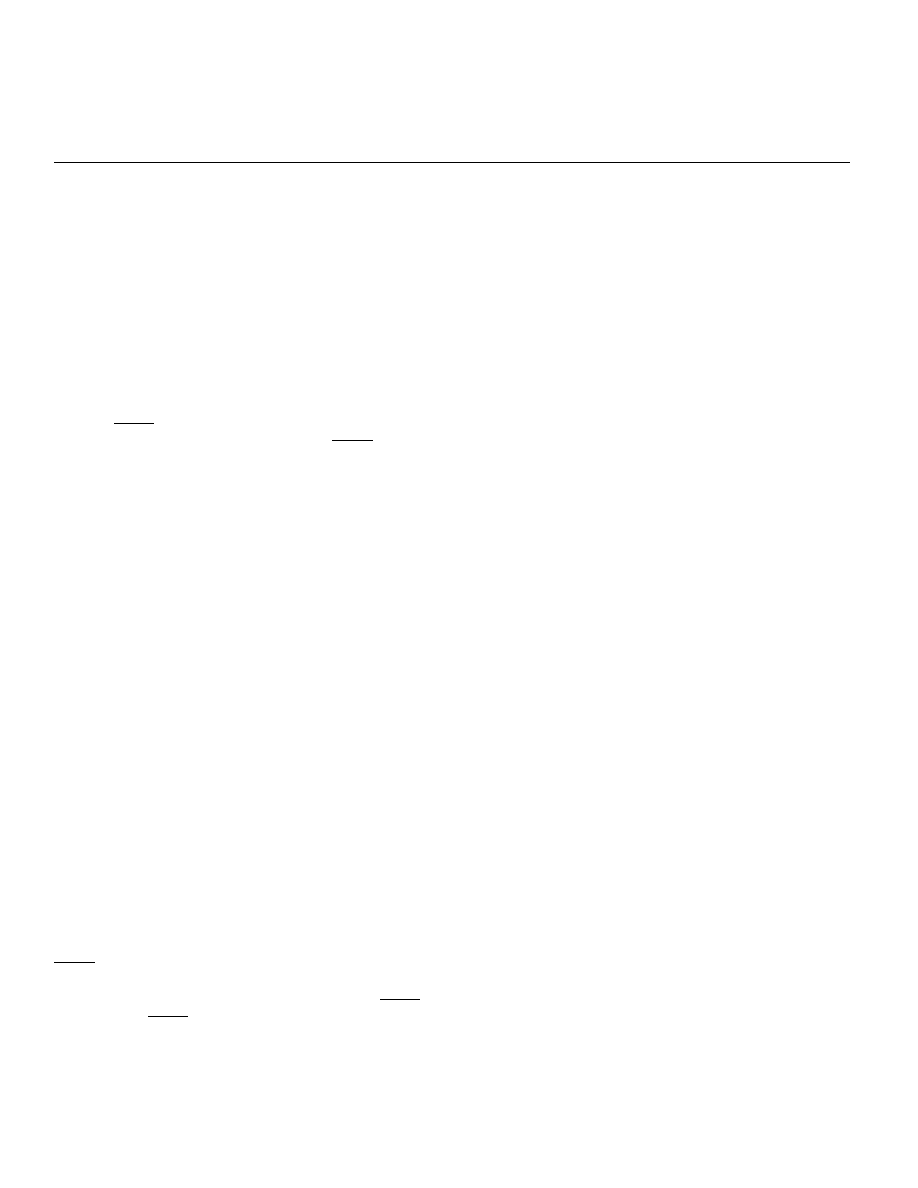
4
PFM/PWM Step-Up DC/DC Controller
TC110
TC110-2 5/24/99
2001 Microchip Technology Inc.
DS21355A
DETAILED DESCRIPTION
TC110 is a PFM/PWM step-up DC/DC controller for use
in systems operating from two or more cells, or in low
voltage, line-powered applications. It uses PWM as the
primary modulation scheme, but automatically converts to
PFM at output duty cycles less than approximately 10%. The
conversion to PFM provides reduced supply current, and
therefore higher operating efficiency at low loads. The
TC110 uses an external switching transistor, allowing con-
struction of switching regulators with maximum output cur-
rents of 300 mA.
The TC110 consumes only 70
A, typical, of supply
current and can be placed in a 0.5
A shutdown mode by
bringing SHDN low. The regulator is disabled during shut-
down, and resumes normal operation when SHDN is brought
high. Other features include start-up at VIN = 0.9V, an
externally-programmable soft start time and tiny 5-pin
SOT-23A packaging.
Operating Mode
The TC110 is powered by the voltage present on the
VDD input. The applications circuits of Figures 1a and 1b
show operation in the bootstrapped and non-bootstrapped
modes. In bootstrapped mode, the TC110 is powered from
the output (start-up voltage is supplied by VIN through the
inductor and Schottky diode while Q1 is off). In bootstrapped
mode, the switching transistor is turned on harder because
its gate voltage is higher (due to the boost action of the
regulator), resulting in higher output current capacity.
The TC110 is powered from the input supply in the non-
bootstrapped mode. In this mode, the supply current to the
TC110 is minimized. However, the drive applied to the gate
of the switching transistor swings from the input supply level
to ground, so the transistor’s ON resistance increases at low
input voltages. Overall efficiency is increased since supply
current is reduced, and less energy is consumed charging
and discharging the gate of the MOSFET. While the TC110
is guaranteed to start up at 0.9V the device performs to
specifications at 2.0V and higher.
Low Power Shutdown Mode
The TC110 enters a low power shutdown mode when
SHDN is brought low. While in shutdown, the oscillator is
disabled and the output switch (internal or external) is shut
off. Normal regulator operation resumes when SHDN is
brought high. SHDN may be tied to the input supply if not
used.
Note: Because the TC110 uses an external diode, a
leakage path between the input voltage and the output node
(through the inductor and diode) exists while the regulator is
in shutdown. Care must be taken in system design to assure
the input supply is isolated from the load during shutdown.
Soft Start
Soft start allows the output voltage to gradually ramp
from 0V to rated output value during start-up. This action
minimizes (or eliminates) overshoot, and in general, re-
duces stress on circuit components. Figure 2 shows the
circuit required to implement soft start. Values of 470K and
0.1
F for RSS and CSS are adequate for most applications.
Input Bypass Capacitors
Using an input bypass capacitor reduces peak current
transients drawn from the input supply, and reduces the
switching noise generated by the regulator. The source
impedance of the input supply determines the size of the
capacitor that should be used.
Output Capacitor
The effective series resistance of the output capacitor
directly affects the amplitude of the output voltage ripple.
(The product of the peak inductor current and the ESR
determines output ripple amplitude.) Therefore, a capacitor
with the lowest possible ESR should be selected. Smaller
capacitors are acceptable for light loads or in applications
where ripple is not a concern. The Sprague 595D series of
tantalum capacitors are amongst the smallest of all low ESR
surface mount capacitors available. Table 1 lists suggested
component numbers and manufacturers.
Inductor Selection
Selecting the proper inductor value is a trade-off be-
tween physical size and power conversion requirements.
Lower value inductors cost less, but result in higher ripple
current and core losses. They are also more prone to
saturate since the coil current ramps to a higher value.
Larger inductor values reduce both ripple current and core
losses, but are larger in physical size and tend to increse the
start-up time slightly.
A 22
H inductor, therefore, is recommended for the 300
KHz versions and a 47
H inductor is recommended for the
100KHz versions. Inductors with a ferrite core (or equiva-
lent) also are recommended. For highest efficiency, use an
inductor with a series resistance less than 20m
.
The inductor value directly affects the output ripple
voltage. Equation 3 is derived as shown below, and can be
used to calculate an inductor value, given the required
output ripple voltage and output capacitor series resistance: