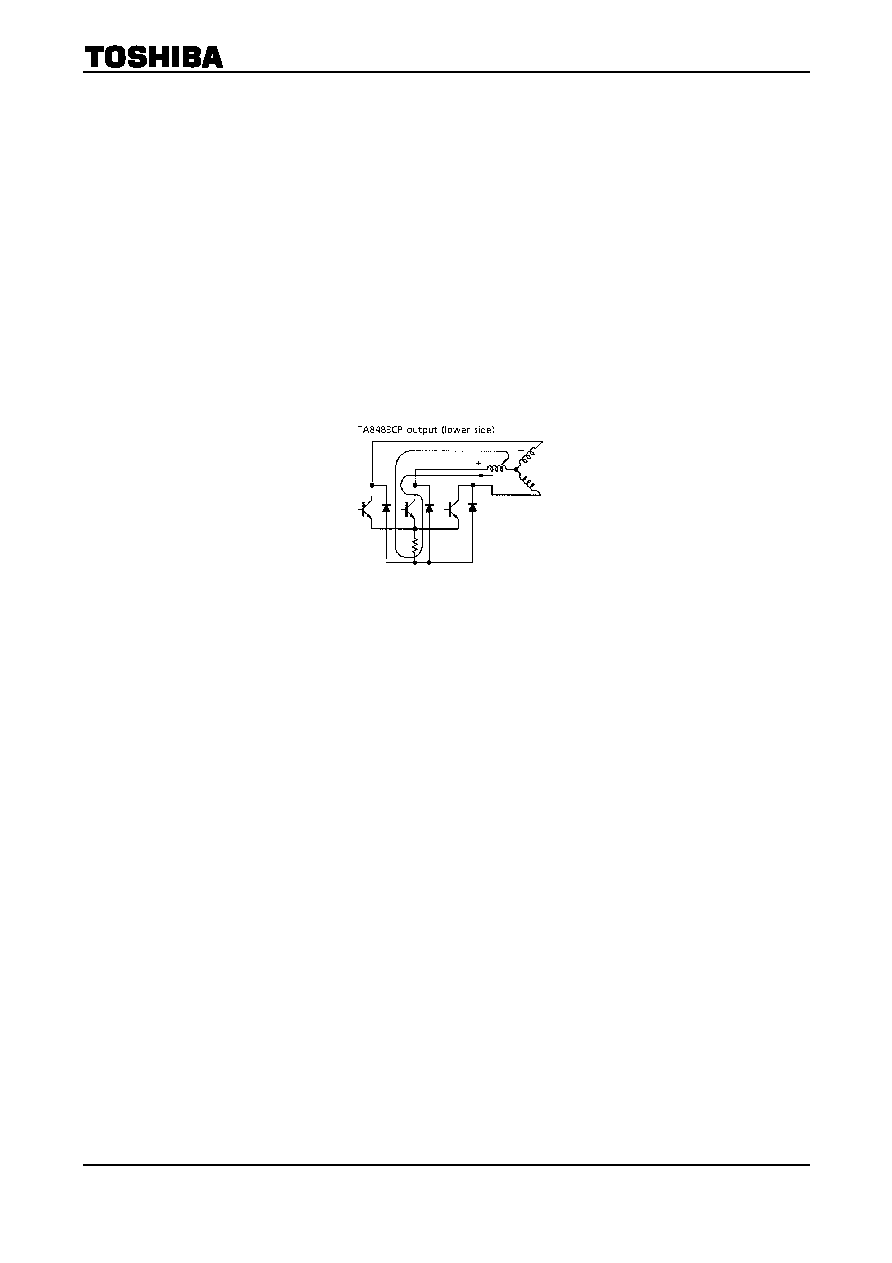
TB6520P/PG
2006-3-6
13
Precautions on Using TB6520P/PG + TA8483CP
About DC Power voltage and control voltage on / off sequence
The poweron sequence dictates that VCC (TA8483CP power supply) be turned on after VDD (TB6520P/PG
power supply) becomes steadily on.
When powering on, make sure VDUTY (PWM control input to the TB6520P/PG) is dropped to 0 V.
When powering off, make sure VDUTY (PWM control input to the TB6520P/PG) is dropped to 0 V.
Before shutting off VDD (TB6520P/PG power supply voltage) wait until VCC (TA8483CP power supply voltage)
is sufficiently low (5 V or less).
The thing that especially requires caution is that shutting off VDD during highspeed rotation or floating GND
causes a shortcircuit current to flow in due to counterelectromotive force, which could break down the output
transistors.
When VDD is shut off, the TB6520P/PG output is pulled to GND and the TA8483CP input goes low, causing all
of the lowerside output transistors to turn on. Because the motor is turning, a shortcircuit current is
generated by counterelectromotive force and flows into the transistors as shown below. This current, if large
enough to exceed the rated current, may break the transistors. (This trouble tends to occur when the motor is
not loaded.)
About an external oscillator for the TB6520P/PG
The TB6520P/PG has an external oscillator attached as the reference clock source to generate PWM control
and commutation signals. Selection of this oscillator requires caution.
Some oscillator may oscillate erratically if the power supply turnon time is fast (1 ms or less), causing the
TB6520P/PG to malfunction. In this case, the drive IC, the TB8483CP, may break down.
(This is because the TB6520P/PG output is uncertain and the overcurrent limiting function becomes unable to
work.)
About the TB6520P/PG DUTY input
When the DUTY pin is open, the duty cycle is full (100%).
If the motor with the TA8483CP connected to it is made to run without turning on the power supply voltage,
the induced voltage in the motor wraps around into the TB6520P/PG, causing it to malfunction, which in turn
may break down the TA8483CP.
Make sure the DUTY pin is pulled low via a resistor (approx. 100 k).
About external diode
For reason of PWM control, when PWM turns off, a regenerative current flows in the lowerside diodes at the
output stage.
Always be sure to attach an external diode. This external diode must have a sufficient current capacity to
satisfy the maximum value of the motor current. Another thing to be noted is that a through current flows
depending on the diode’s reverse recovery time.
Toshiba recommends attaching a Schottky diode (2GWJ42 or equivalent).