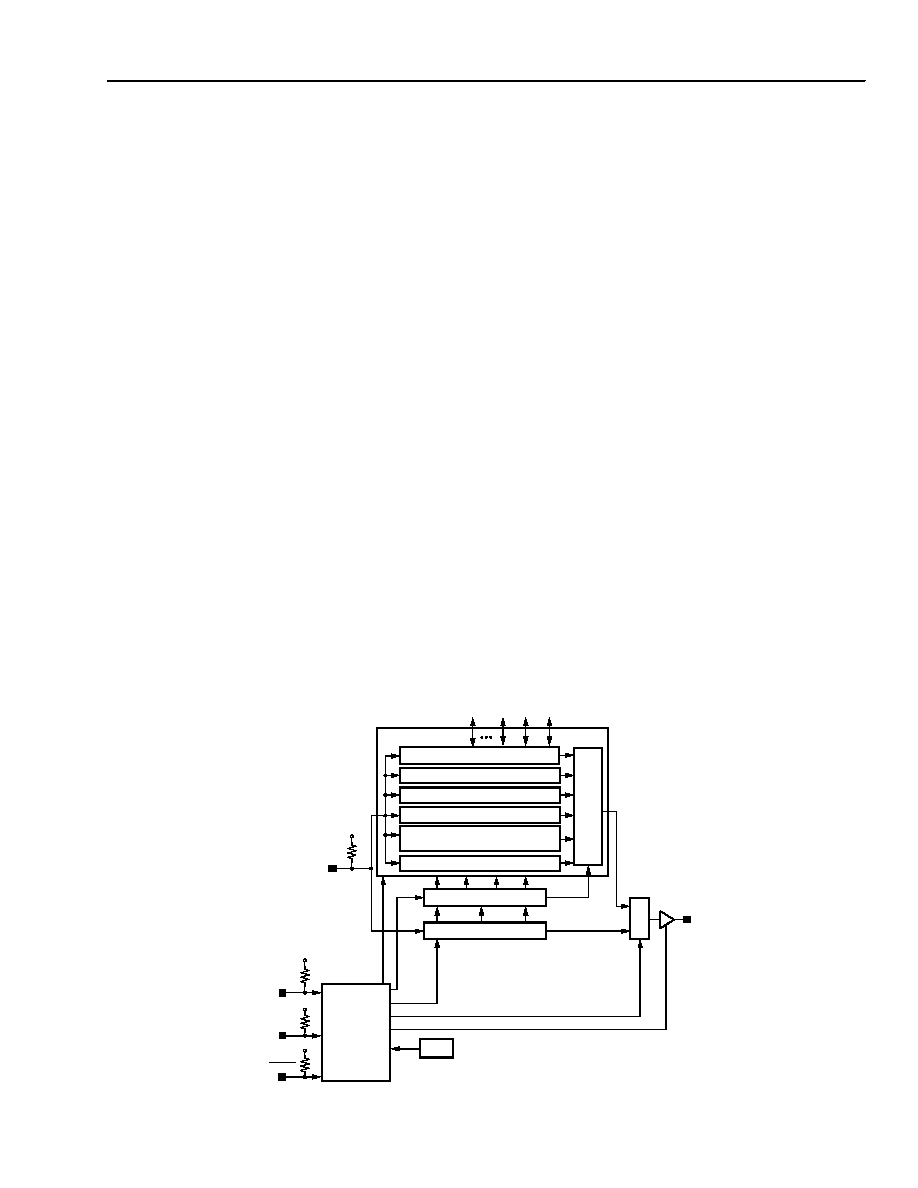
Preliminary Data Sheet, Rev. 1
September 1998
ORCA Series 3 FPGAs
Lucent Technologies Inc.
57
Special Function Blocks (continued)
ORCA Boundary-Scan Circuitry
The
ORCA Series boundary-scan circuitry includes a
test access port controller (TAPC), instruction register
(IR), boundary-scan register (BSR), and bypass regis-
ter. It also includes circuitry to support the four pre-
defined instructions.
Figure 38 shows a functional diagram of the boundary-
scan circuitry that is implemented in the
ORCA Series.
The input pins’ (TMS, TCK, and TDI) locations vary
depending on the part, and the output pin is the dedi-
cated TDO/RD_DATA output pad. Test data in (TDI) is
the serial input data. Test mode select (TMS) controls
the boundary-scan test access port controller (TAPC).
Test clock (TCK) is the test clock on the board.
The BSR is a series connection of boundary-scan cells
(BSCs) around the periphery of the IC. Each I/O pad on
the FPGA, except for CCLK, DONE, and the boundary-
scan pins (TCK, TDI, TMS, and TDO), is included in
the BSR. The first BSC in the BSR (connected to TDI)
is located in the first PIC I/O pad on the left of the top
side of the FPGA (PTA PIC). The BSR proceeds clock-
wise around the top, right, bottom, and left sides of the
array. The last BSC in the BSR (connected to TDO) is
located on the top of the left side of the array (PL1D).
The bypass instruction uses a single FF, which resyn-
chronizes test data that is not part of the current scan
operation. In a bypass instruction, test data received on
TDI is shifted out of the bypass register to TDO. Since
the BSR (which requires a two FF delay for each pad)
is bypassed, test throughput is increased when devices
that are not part of a test operation are bypassed.
The boundary-scan logic is enabled before and during
configuration. After configuration, a configuration
option determines whether or not boundary-scan logic
is used.
The 32-bit boundary-scan identification register con-
tains the manufacturer’s ID number, unique part num-
ber, and version (as described earlier). The
identification register is the default source for data on
TDO after RESET if the TAP controller selects the shift-
data-register (SHIFT DR) instruction. If boundary scan
is not used, TMS, TDI, and TCK become user
I/Os, and TDO is 3-stated or used in the readback
operation.
An optional USERCODE is available if the boundary-
scan PSR1 instruction is not used. The selection
between PSR1 and USERCODE is a configuration
option and can be performed in
ORCA Foundry. The
USERCODE is an 11-bit value that the user can set
during device configuration and can be written to and
read from the FPGA via the boundary-scan logic. The
USERCODE value replaces the manufacturer field of
the boundary-scan ID code when the USERCODE
instruction is issued, allowing users to have configured
devices identified in a user-defined manner. The manu-
facturer ID field remains available when the IDCODE
instruction is issued.
Figure 38.
ORCA Series Boundary-Scan Circuitry Functional Diagram
TAP
CONTROLLER
TMS
TCK
BOUNDARY-SCAN REGISTER
PSR2 REGISTER (PLCs)
BYPASS REGISTER
DATA
MUX
INSTRUCTION DECODER
INSTRUCTION REGISTER
M
U
X
RESET
CLOCK IR
SHIFT IR
UPDATE IR
PUR
TDO
SELECT
ENABLE
RESET
CLOCK DR
SHIFT DR
UPDATE DR
TDI
DATA REGISTERS
PSR1/USERCODE REGISTER
CONFIGURATION REGISTER
(RAM_R, RAM_W)
PRGM
I/O BUFFERS
VDD
IDCODE REGISTER
5-5768(F)