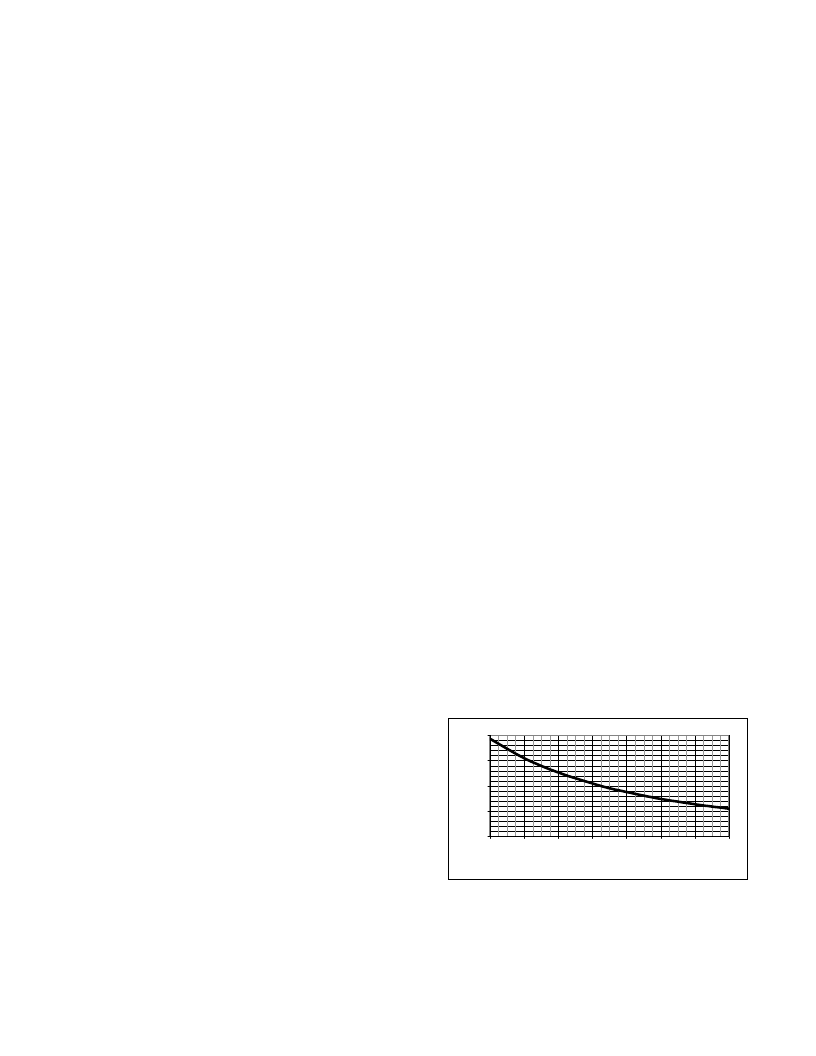
THEORY OF OPERATION
The MEMSIC device is a complete dual-axis acceleration
measurement system fabricated on a monolithic CMOS IC
process. The device operation is based on heat transfer by
natural convection and operates like other accelerometers
having a proof mass. The stationary element, or ‘proof
mass’, in the MEMSIC sensor is a gas.
A single heat source, centered in the silicon chip is
suspended across a cavity. Equally spaced
aluminum/polysilicon thermopiles (groups of
thermocouples) are located equidistantly on all four sides of
the heat source (dual axis). Under zero acceleration, a
temperature gradient is symmetrical about the heat source,
so that the temperature is the same at all four thermopiles,
causing them to output the same voltage.
Acceleration in any direction will disturb the temperature
profile, due to free convection heat transfer, causing it to be
asymmetrical. The temperature, and hence voltage output
of the four thermopiles will then be different. The
differential voltage at the thermopile outputs is directly
proportional to the acceleration. There are two identical
acceleration signal paths on the accelerometer, one to
measure acceleration in the x-axis and one to measure
acceleration in the y-axis. Please visit the MEMSIC
website at www.memsic.com for a picture/graphic
description of the free convection heat transfer principle.
PIN DESCRIPTIONS
V
DD
– This is the supply input for the digital circuits and
the sensor heater in the accelerometer. The DC voltage
should be between 2.70 and 5.25 volts. Refer to the section
on PCB layout and fabrication suggestions for guidance on
external parts and connections recommended.
V
DA
– This is the power supply input for the analog
amplifiers in the accelerometer. Refer to the section on
PCB layout and fabrication suggestions for guidance on
external parts and connections recommended.
Gnd
– This is the ground pin for the accelerometer.
A
OUTX
– This pin is the output of the x-axis acceleration
sensor. The user should ensure the load impedance is
sufficiently high as to not source/sink >100
μ
A. While the
sensitivity of this axis has been programmed at the factory
to be the same as the sensitivity for the y-axis, the
accelerometer can be programmed for non-equal
sensitivities on the x- and y-axes. Contact the factory for
additional information on this feature.
A
OUTY
–
This pin is the output of the y-axis acceleration
sensor. The user should ensure the load impedance is
sufficiently high as to not source/sink >100
μ
A. While the
sensitivity of this axis has been programmed at the factory
to be the same as the sensitivity for the x-axis, the
accelerometer can be programmed for non-equal
MEMSIC MXA2500U Rev A
Page 4 of
8
05/02
sensitivities on the x- and y-axes. Contact the factory for
additional information on this feature.
T
OUT
– This pin is the buffered output of the temperature
sensor. The analog voltage at T
OUT
is an indication of the
die temperature. This voltage is useful as a differential
measurement of temperature from ambient and not as an
absolute measurement of temperature. After correlating the
voltage at T
OUT
to 25
°
C ambient, the change in this voltage
due to changes in the ambient temperature can be used to
compensate for the change over temperature of the
accelerometer offset and sensitivity. Please refer to the
section on Compensation for the Change in Sensitivity
Over Temperature for more information.
Sck
– The standard product is delivered with an internal
clock option (800kHz).
This pin should be grounded
when operating with the internal clock.
An external
clock option can be special ordered from the factory
allowing the user to input a clock signal between 400kHz
and 1.6MHz.
V
ref
– A reference voltage is available from this pin. It is
set at 2.50V typical and has 100
μ
A of drive capability.
COMPENSATION FOR THE CHANGE IN
SENSITIVITY OVER TEMPERATURE
All thermal accelerometers display the same sensitivity
change with temperature. The sensitivity change depends
on variations in heat transfer that are governed by the laws
of physics. Manufacturing variations do not influence the
sensitivity change, so there are no unit-to-unit differences
in sensitivity change. The sensitivity change is governed
by the following equation (and shown in Figure 1 in
°
C):
S
i
x T
i
where S
i
is the sensitivity at any initial temperature T
i
, and
S
f
is the sensitivity at any other final temperature T
f
with
the temperature values in
°
K.
2.81
= S
f
x T
f
2.81
0.0
0.5
1.0
1.5
2.0
-40
-20
0
20
40
60
80
100
Temperature (C)
S
Figure 1: Thermal Accelerometer Sensitivity
In gaming applications where the game or controller is
typically used in a constant temperature environment,
sensitivity might not need to be compensated in hardware