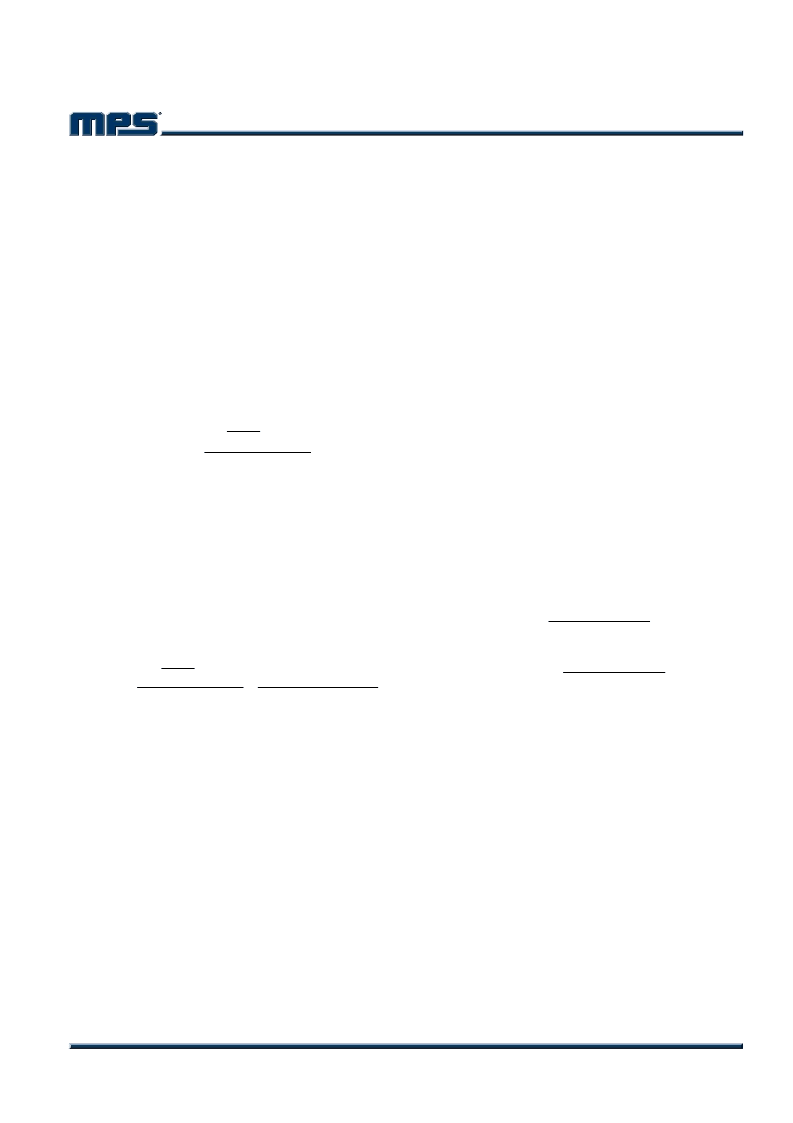
MP1542 – 700KHz/1.3MHz BOOST CONVERTER WITH A 2A SWITCH
MP1542 Rev. 1.3
9/7/2006
www.MonolithicPower.com
7
MPS Proprietary Information. Unauthorized Photocopy and Duplication Prohibited.
2006 MPS. All Rights Reserved.
Selecting the Output Capacitor
The output capacitor is required to maintain the
DC output voltage. Low ESR capacitors are
preferred to keep the output voltage ripple to a
minimum. The characteristic of the output
capacitor also affects the stability of the
regulation control system. Ceramic, tantalum, or
low
ESR
electrolytic
recommended.
In
the
capacitors, the impedance of the capacitor at
the switching frequency is dominated by the
capacitance, and so the output voltage ripple is
mostly independent of the ESR. The output
voltage ripple is estimated to be:
capacitors
case
are
of
ceramic
SW
LOAD
OUT
2
C
IN
RIPPLE
V
f
I
V
V
-
×
×
≈
Where V
RIPPLE
is the output ripple voltage, V
IN
and V
OUT
are the DC input and output voltages
respectively, I
LOAD
is the load current, f
SW
is the
switching frequency, and C2 is the capacitance
of the output capacitor.
In the case of tantalum or low-ESR electrolytic
capacitors, the ESR dominates the impedance
at the switching frequency, and so the output
ripple is calculated as:
IN
OUT
V
ESR
V
LOAD
SW
LOAD
OUT
2
C
IN
RIPPLE
V
R
I
f
I
)
V
V
1
×
×
+
×
×
≈
Where R
ESR
is the equivalent series resistance
of the output capacitors.
Choose an output capacitor to satisfy the output
ripple and load transient requirements of the
design. A 4.7μF-22μF ceramic capacitor is
suitable for most applications.
Selecting the Inductor
The inductor is required to force the higher
output voltage while being driven by the input
voltage. A larger value inductor results in less
ripple current that results in lower peak inductor
current, reducing stress on the internal
N-Channel
.
switch. However, the larger value
inductor has a larger physical size, higher
series resistance, and/or lower saturation
current.
A 4.7
μ
H inductor is recommended for most
1.3MHz applications and a 10
μ
H inductor is
recommended for most 700KHz applications.
However, a more exact inductance value can
be calculated. A good rule of thumb is to allow
the
peak-to-peak
ripple
approximately 30-50% of the maximum input
current. Make sure that the peak inductor
current is below 75% of the current limit at the
operating duty cycle to prevent loss of
regulation due to the current limit. Also make
sure that the inductor does not saturate under
the worst-case load transient and startup
conditions. Calculate the required inductance
value by the equation:
current
to
be
I
f
×
V
)
V
-
×
(V
×
V
L
SW
OUT
IN
OUT
IN
=
η
×
)
I
×
=
IN
)
MAX
(
LOAD
I
OUT
V
)
MAX
(
IN
I
V
(
)
MAX
(
IN
%
50
%
30
I
=
Where I
LOAD(MAX)
is the maximum load current,
I
is the peak-to-peak inductor ripple current, and
η
is efficiency.
Selecting the Diode
The output rectifier diode supplies current to the
inductor when the internal MOSFET is off. To
reduce losses due to diode forward voltage and
recovery time, use a Schottky diode with the
MP1542. The diode should be rated for a
reverse voltage equal to or greater than the
output voltage used. The average current rating
must be greater than the maximum load current
expected, and the peak current rating must be
greater than the peak inductor current.