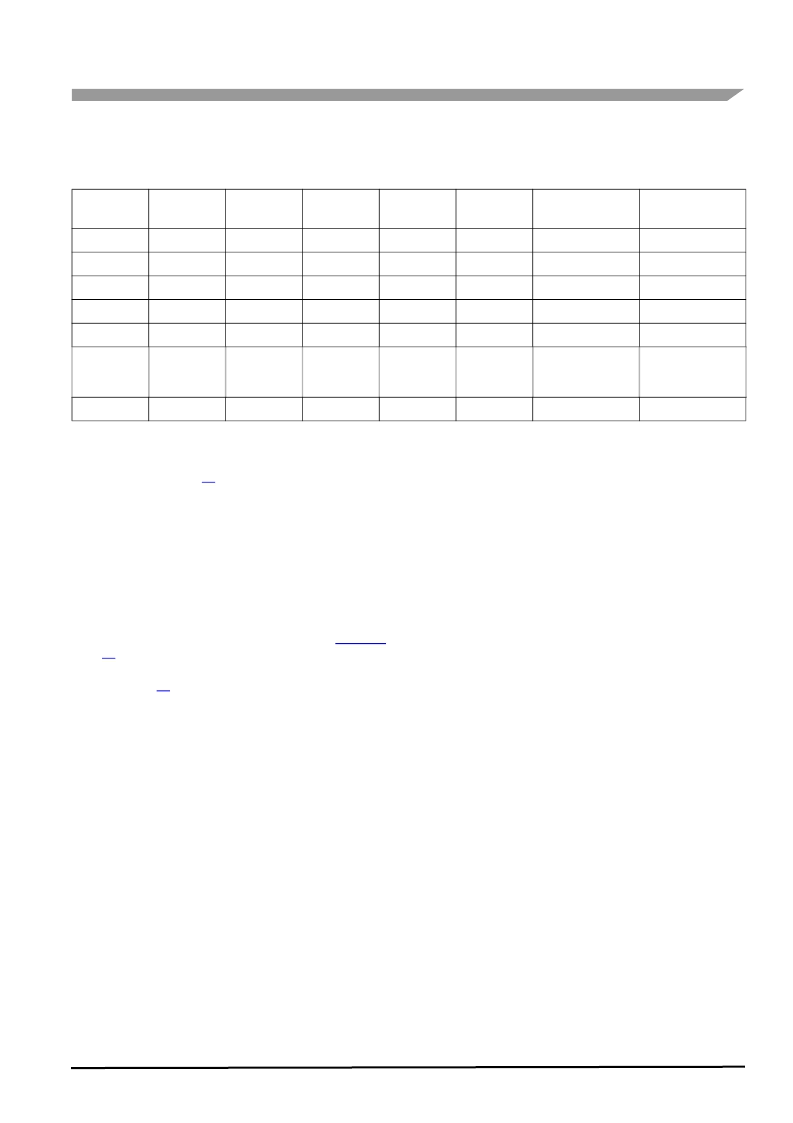
Analog Integrated Circuit Device Data
Freescale Semiconductor
19
33976
FUNCTIONAL DEVICE OPERATION
LOGIC COMMANDS AND REGISTERS
Address 110 — Ramp Selection Register (RMPSELR)
SI Address 110 Ramp Selection Register (RMPSELR)
(refer to
Table 15
, page
20
). A write to the 33976 using this
register allows the master to independently modify the
pointer movement response characteristics of each gauge
driver. The user has three variables that can be configured,
during the initialization of the device, to provide quick and
responsive pointers (e.g., tachometer applications) or soft
landing and less responsive pointers (e.g., speedometer or
fuel indicators). These three variables are (1) the ramp zero
selection RS (RS3:RS0), (2) the hold count cut-in location
offset variable HCP (HCP2: HCP0), and (3) the hold count
value HC, (HC3:HC0). Each of these variables is described
below and an implementation example is shown in
Figure 11
,
page
31
.
The state machine uses the velocity ramp (refer to
Table 30
, page
28
) to control the acceleration, deceleration
and speed of the pointer movement. During an acceleration
from a stopped position, the state machine will microstep the
pointer at each velocity step, starting with step 0, in
succession until the desired pointer speed is reached.
Similarly, as the pointer approaches the commanded
position, the state machine will microstep the motor at
successive velocity steps down the velocity ramp until
reaching step 0. The fastest that a pointer can accelerate,
decelerate or change directions is limited by the velocity
ramp.
For example, if a pointer is moving in the clockwise
direction and is commanded to a position that is counter
clockwise from the current pointer location, then the state
machine must first decelerate the pointer down the ramp to
the step 0 location, change directions and then accelerate up
the ramp towards the commanded location. In this situation,
the state machine will force movement down and then up the
ramp as fast as possible by stepping at each Velocity Position
only once for a direction change. The low velocity steps (e.g.,
Velocity Position 1 is 27 ms) are significant in that they can
limit the speed with which a pointer can change direction.
Bits RS3:RS0 of the RMPSELR are used to truncate as
many as 15 velocity steps off of the bottom of the velocity
ramp. The value of RS determines the Initial Velocity Ramp
Position:
Initial Velocity Position = RS + 1
For example, writing a value of 4 to these bits truncates the
velocity ramp by 4 and would result in a first and last velocity
step of 5.86ms (Velocity Position 5). A pointer will change
directions much faster with this abbreviated ramp than it
would if using the default ramp with a Velocity Position 1 of
27 ms
Most applications require a smooth dynamic pointer as the
commanded position is constantly updated. Movement along
the ramp at the maximum acceleration and deceleration (only
one step at each velocity position) results in a choppy
movement because the movement velocity range is large for
small changes in position as the pointer quickly reaches
commanded locations from command to command.
Configuring the state machine to repeat velocity steps at
several of the last few step locations, when the pointer
decelerates to the commanded location, can eliminate this
choppy movement. These repetitive steps are referred to as
hold counts.
Bits HCP2: HCP0 of the RMPSELR determine the velocity
step location at which the hold counts begin during a
deceleration to the commanded position. The value written to
HCP2: HCP0 (HCP) is multiplied by 8 and added to the RS
value. The result is the first velocity position, or the Hold
Count Cut-In Point, to which the hold counts will apply during
a deceleration.
First Velocity Position w/ Hold Counts = HCP x 8 + RS
The exception to this is when the HCP2: HCP0 value is
000. In this case, HCP = 8 and the cut-in point will be 64 steps
above the RS value. The default value of the HCP = 2 or a
hold count cut-in point of 16 velocity steps above the RS
value.
Table 14. RTZCR Accumulator Offset
RC10
RC9
RC8
RC7
RC6
RC5
Preload Value
(PV)
Initial Accumulator
Value = (-16 x PV) -1
0
0
0
0
0
0
0
-1
0
0
0
0
0
1
1
-17
0
0
0
0
1
0
2
-33
0
0
0
0
1
1
3
-49
0
0
0
1
0
0
4
-65
.
.
.
.
.
.
.
.
.
.
.
.
.
.
.
.
.
.
.
.
.
.
.
.
1
1
1
1
1
1
63
-1009