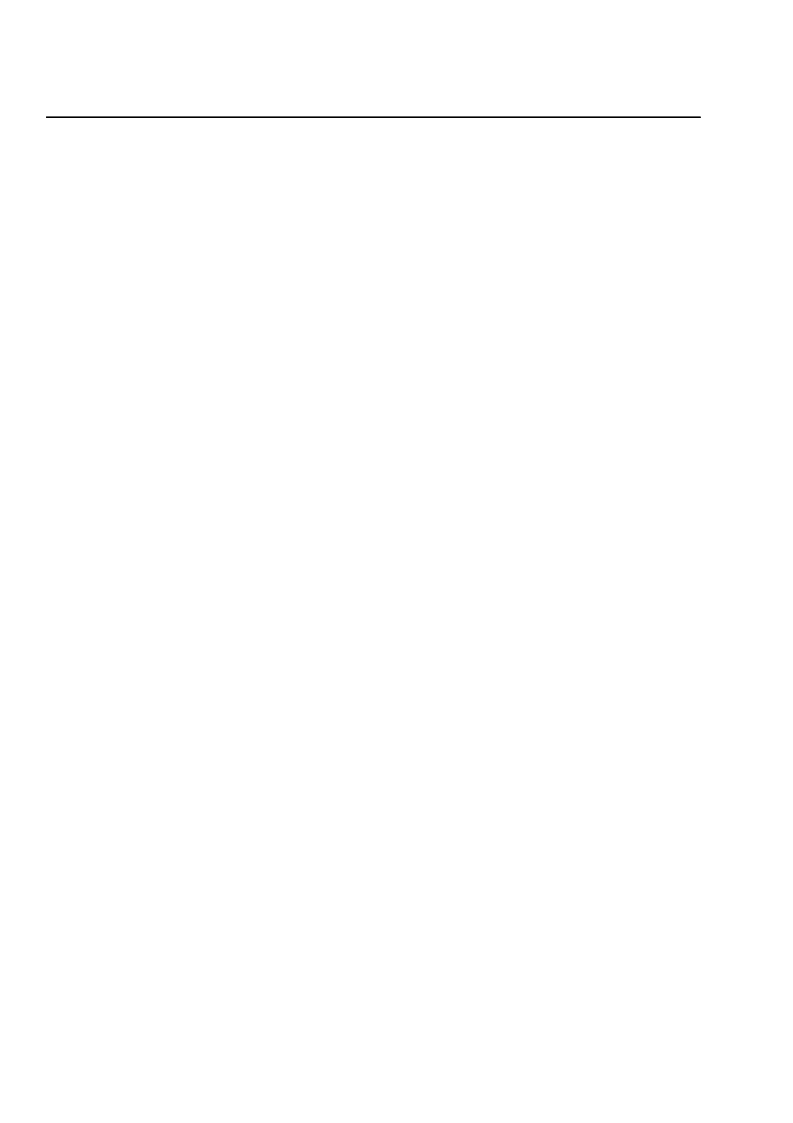
8
Tyco Electronics Corp.
Advance Data Sheet
March 1999
36 Vdc to 75 Vdc Inputs; 25 W
LW025 Single-Output-Series Power Modules:
Design Considerations
Grounding Considerations
For modules without the isolated case ground pin
option, the case is internally connected to the V
I
(+) pin.
For modules with the isolated case ground pin, device
code suffix “7,” the V
I
(+) pin is not connected to the
case.
Input Source Impedance
The power module should be connected to a low ac-
impedance input source. Highly inductive source
impedances can affect the stability of the power mod-
ule. For the test configuration in Figure 10, a 33 μF
electrolytic capacitor (ESR < 0.7 at 100 kHz)
mounted close to the power module helps ensure sta-
bility of the unit. For other highly inductive source
impedances, consult the factory for further application
guidelines.
Safety Considerations
For safety-agency approval of the system in which the
power module is used, the power module must be
installed in compliance with the spacing and separation
requirements of the end-use safety agency standard,
i.e., UL 1950, CSAC22.2 No. 950-95, and VDE 0805
(EN60950, IEC950).
If the input source is non-SELV (ELV or a hazardous
voltage greater than 60 Vdc and less than or equal to
75 Vdc), for the module's output to be considered
meeting the requirements of safety extra-low voltage
(SELV), all of the following must be true:
■
The input source is to be provided with reinforced
insulation from any other hazardous voltages, includ-
ing the ac mains; and
■
One V
I
pin and one V
O
pin are to be grounded or
both the input and output pins are to be kept floating;
and
■
The input pins of the module are not operator acces-
sible; and
■
Another SELV reliability test is conducted on the
whole system, as required by the safety agencies, on
the combination of supply source and the subject
module to verify that under a single fault, hazardous
voltages do not appear at the module's output.
Note:
Do not ground either of the input pins of the
module without grounding one of the output
pins. This may allow a non-SELV voltage to
appear between the output pins and ground.
The power module has extra-low voltage (ELV) outputs
when all inputs are ELV.
The input to these units is to be provided with a maxi-
mum 5 A normal-blow fuse in the ungrounded lead.
Feature Descriptions
Overcurrent Protection
To provide protection in a fault (output overload) condi-
tion, the unit is equipped with internal current-limiting
circuitry and can endure current limiting for an unlim-
ited duration. At the point of current-limit inception, the
unit shifts from voltage control to current control. If the
output voltage is pulled very low during a severe fault,
the current-limit circuit can exhibit either foldback or
tailout characteristics (output-current decrease or
increase). The unit operates normally once the output
current is brought back into its specified range.
Remote On/Off
Two remote on/off options are available. Positive logic
remote on/off turns the module on during a logic-high
voltage on the REMOTE ON/OFF pin, and off during a
logic low. Negative logic, device code suffix “1,” remote
on/off turns the module off during a logic high and on
during a logic low.
To turn the power module on and off, the user must
supply a switch to control the voltage between the
on/off terminal and the V
I
(–) terminal (V
on/off
). The
switch can be an open collector or equivalent (see Fig-
ure 13). A logic low is V
on/off
= –0.7 V to 1.2 V. The max-
imum I
on/off
during a logic low is 1 mA. The switch
should maintain a logic-low voltage while sinking 1 mA.
During a logic high, the maximum V
on/off
generated by
the power module is 6 V. The maximum allowable leak-
age current of the switch at V
on/off
= 6 V is 50 μA.
The module has internal capacitance to reduce noise
at the ON/OFF pin. Additional capacitance is not gen-
erally needed and may degrade the start-up character-
istics of the module.