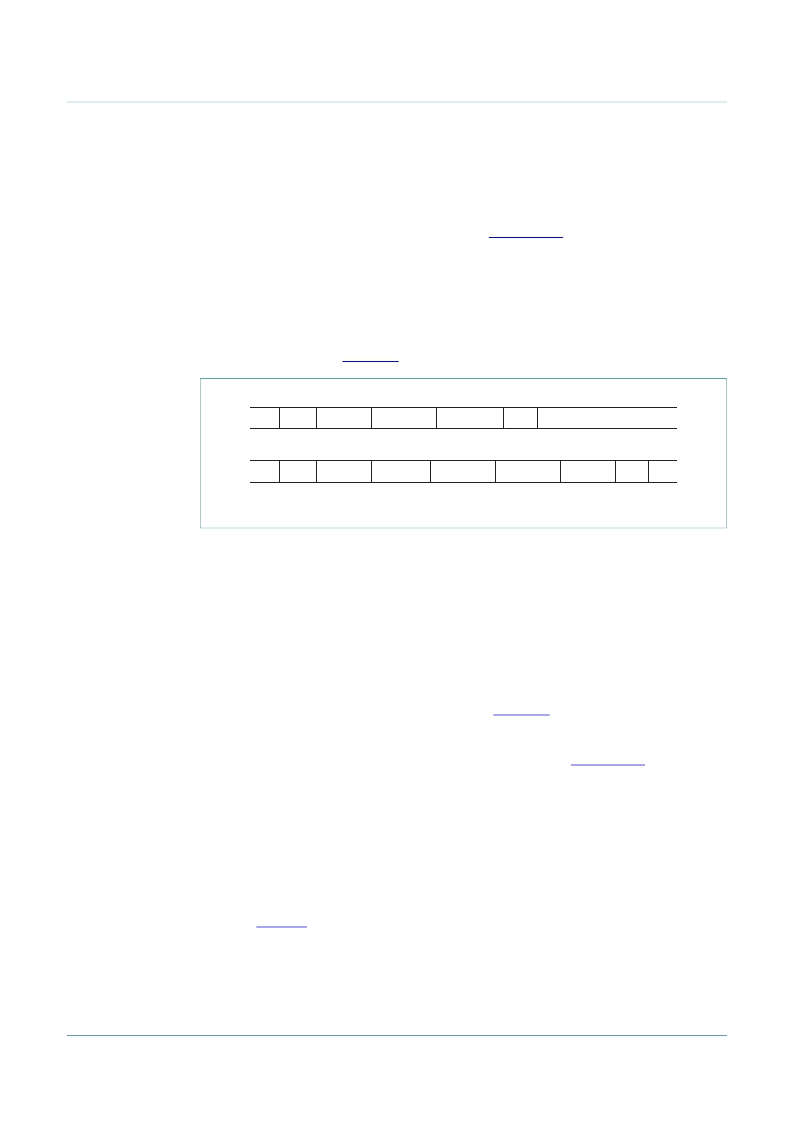
KMA210
All information provided in this document is subject to legal disclaimers.
NXP B.V. 2011. All rights reserved.
Product data sheet
Rev. 1 — 30 June 2011
17 of 36
NXP Semiconductors
KMA210
Programmable angle sensor
Command mode has to be entered to enable programming. In this mode, the customer
can adjust all required parameters (for example zero angle and angular range) to meet the
application requirements. After enabling the internal charge pump and waiting for t
cp
the
data is stored in the non-volatile memory. After changing the contents of the memory, the
checksum must be recalculated and written (see
Section 13.4
).
In order to enter the command mode, a specific command sequence must be sent after a
power-on reset and during the time slot t
cmd(ent)
. The external source used to send the
command sequence must overdrive the output buffer of the KMA210. In doing so it
provides current I
od
.
During communication, the KMA210 is always the slave and the external programming
hardware is the master.
Figure 12
illustrates the structure of the OWI data format.
The master provides the start condition, which is a rising edge after a LOW level. Then a
command byte which can be either a read or a write command is sent. Depending on the
command, the master or the slave has to send the data immediately after the command
sequence. In the case of a read command, an additional handover or takeover bit is
inserted before and after the data bytes. Each communication must be closed with a stop
condition driven by the master. If the slave does not receive a rising edge for a time longer
than t
to
, a time-out condition occurs. The bus is reset to the idle state and waits for a start
condition and a new command. This can be used to synchronize the device regardless of
the previous state.
All communication is based on this structure (see
Figure 12
), even for entering the
command mode. In this case a special write command is required, followed by the
command sequence (two data bytes). The customer can access the non-volatile memory,
CTRL1, TESTCTRL0 and SIGNATURE registers (described in
Section 13.5
). Only a
power-on reset will leave the command mode. A more detailed description of the
programming is given in the next sections.
13.2 Timing characteristics
As described in the previous section, a start and stop condition is necessary for
communication. The LOW-level duration before the rising edge of the start condition is
defined as t
start
. The HIGH-level duration after the rising edge of the stop condition is
defined as t
stop
. These parameters, together with all other timing characteristics are
shown in
Table 14
.
Fig 12. OWI data format
001aag742
write
IDLE
IDLE
START
STOP
COMMAND DATA BYTE 1 DATA BYTE 2
IDLE
START COMMAND HANDOVER
TAKEOVER STOP
IDLE
DATA BYTE 1 DATA BYTE 2
read