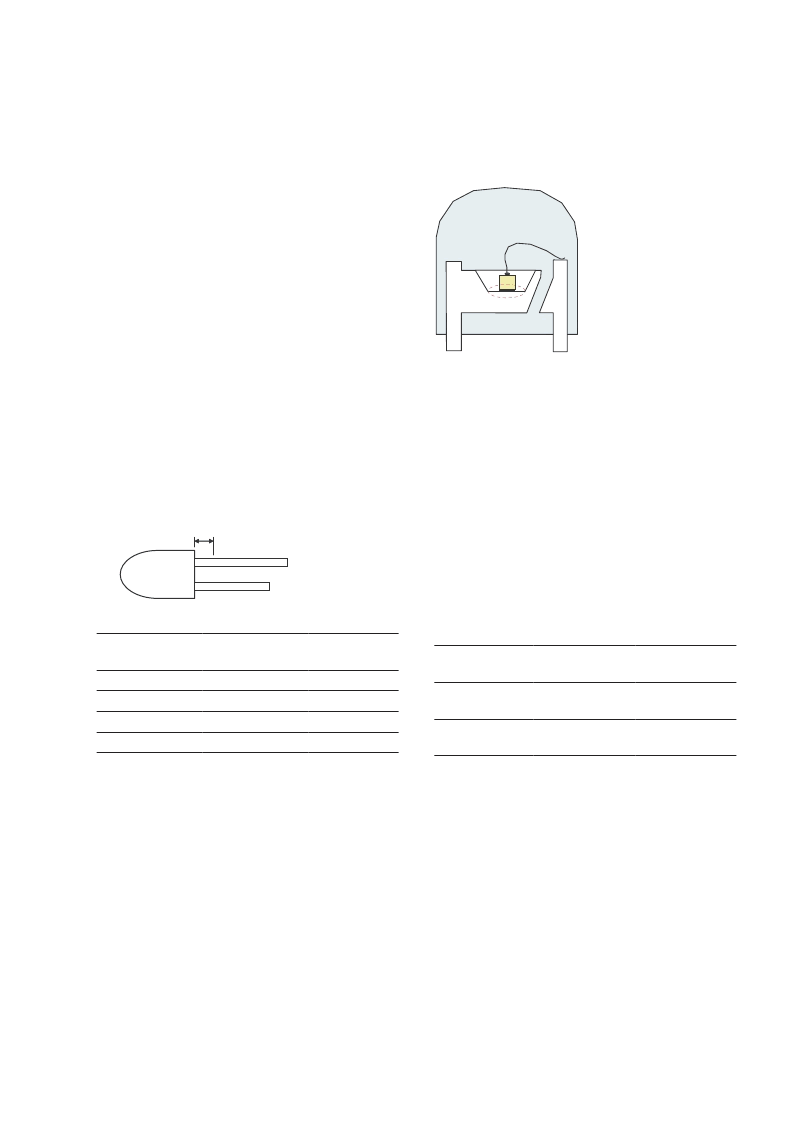
7
Avago Technologies LED configuration
Precautions:
Lead Forming:
TheleadsofanLEDlampmaybeperformedorcutto
lengthpriortoinsertionandsolderingonPCboard.
Ifleadformingisrequiredbeforesoldering,caremust
betakentoavoidanyexcessivemechanicalstressthat
induced into the LED package. Otherwise, cut the
leadstoapplicablelengthaftersolderingprocessat
roomtemperature.Thesolderjointformedwillabsorb
themechanicalstress,duetotheleadcutting,from
travelingtotheLEDchipdieattachandwirebond.
Forbettercontrol,itisrecommendedtouseproper
tooltopreciselyformandcuttheleadstoapplicable
lengthratherthandoingitmanually.
Soldering condition:
Care must be taken during PCB assembly and
soldering process to prevent damage to the LED
component.
Theclosestmanualsolderingdistanceofthesoldering
heat source (soldering iron’s tip) to the body is
1.59mm.SolderingtheLEDcloserthan1.59mmmight
damagetheLED.
Recommendedsolderingcondition:
Wave Soldering
05 °C Max.
30 sec Max
50 °C Max.
3 sec Max.
Manual Solder
Dipping
-
-
60 °C Max.
5 sec Max
Pre-heat temperature
Preheat time
Peak temperature
Dwell time
Wavesolderingparametermustbesetandmaintain
according to the recommended temperature and
dwelltime.Customerisadvisedtodailycheckonthe
solderingprofiletoensurethatthesolderingprofile
is always conforming to recommended soldering
condition.
Note:
1. PCB with different size and design (component density) will
have different heat mass (heat capacity). This might cause a
changeintemperatureexperiencedbytheboardifsamewave
solderingsettingisused.So,itisrecommendedtore-calibrate
thesolderingprofileagainbeforeloadinganewtypeofPCB.
2. Avago Technologies’ high brightness LED are using high
efficiency LED die with single wire bond as shown below.
Customer is advised to take extra precaution during wave
soldering to ensure that the maximum wave temperature is
notexceeding250°C.Over-stressingtheLEDduringsoldering
process might cause premature failure to the LED due to
delamination.
1.59mm
Note:ElectricalconnectionbetweenbottomsurfaceofLEDdieand
theleadframematerialthroughconductivepasteofsolder.
Ifnecessary,usefixturetoholdtheLEDcomponent
inproperorientationwithrespecttothePCBduring
solderingprocess.
Atelevatedtemperature,theLEDismoresusceptible
tomechanicalstress.Therefore,PCBmustallowedto
cool down to room temperature prior to handling,
whichincludesremovalofjigs,fixturesorpallet.
Specialattentionmustbegiventoboardfabrication,
soldermasking,surfaceplattingandleadholessize
andcomponentorientationtoassurethesolderability.
RecommendedPCboardplatedthroughholessizefor
LEDcomponentleads.
LED component
lead size
0.457 x 0.457 mm
(0.08 x 0.08 inch)
0.508 x 0.508 mm
(0.00 x 0.00 inch)
Diagonal
0.646 mm
(0.05 inch)
0.78 mm
(0.08 inch)
Plated through
hole diameter
0.976 to .078 mm
(0.038 to 0.04 inch)
.049 to .50 mm
(0.04 to 0.045 inch)
Under sizing of plated through hole can lead to
twisting or improper LED placement during auto
insertion.Oversizingplatedthroughholecanleadto
mechanicalstressontheepoxylensduringclinching.
Note: Refer to application note AN1027 for more information on
solderingLEDcomponents.
InGaN Device
Anode