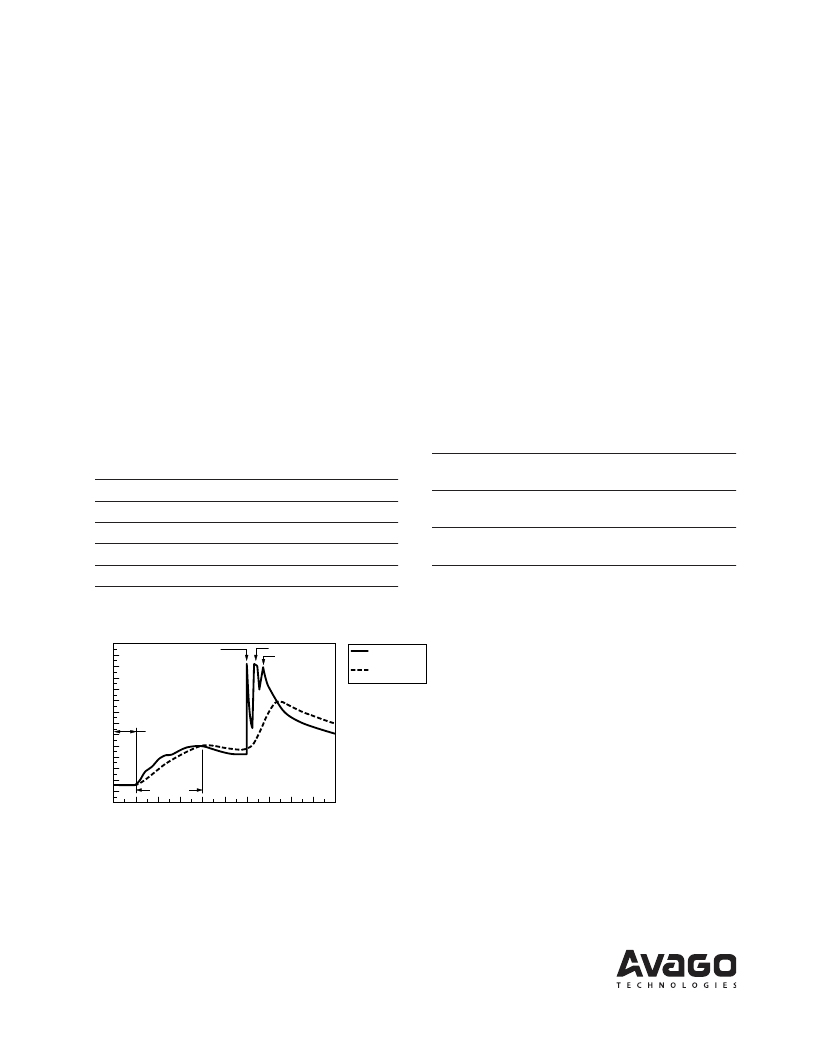
Precautions:
Lead Forming
TheleadsofanLEDlampmaybepreformedorcutto
lengthpriortoinsertionandsolderingintoPCboard.
Ifleadformingisrequiredbeforesoldering,caremust
be taken to avoid any excessive mechanical stress
induced to LED package. Otherwise, cut the leads
of LED to length after soldering process at room
temperature.Thesolderjointformedwillabsorbthe
mechanicalstressoftheleadcuttingfromtravelingto
theLEDchipdieattachandwirebond.
Itisrecommendedthattoolingmadetopreciselyform
andcuttheleadstolengthratherthanrelyuponhand
operation.
Soldering Conditions
CaremustbetakenduringPCBassemblyandsoldering
processtopreventdamagetoLEDcomponent.
TheclosestLEDisallowedtosolderonboardis1.59
mm below the body (encapsulant epoxy) for those
partswithoutstandoff.
Recommendedsolderingconditions:
Wavesolderingparametermustbesetandmaintained
according to recommended temperature and dwell
time in the solder wave. Customer is advised to
periodicallycheckonthesolderingprofiletoensure
the soldering profile used is always conforming to
recommendedsolderingcondition.
Ifnecessary,usefixturetoholdtheLEDcomponent
inproperorientationwithrespecttothePCBduring
solderingprocess.
Proper handling is imperative to avoid excessive
thermal stresses to LED components when heated.
Therefore,thesolderedPCBmustbeallowedtocoolto
roomtemperature,5°C,beforehandling.
Specialattentionmustbegiventoboardfabrication,
soldermasking,surfaceplatingandleadholessizeand
componentorientationtoassuresolderability.
RecommendedPCboardplatedthroughholesizesfor
LEDcomponentleads:
Wave Soldering
Dipping
Manual Solder
Pre-heatTemperature 105°CMax.
–
Pre-heatTime
30secMax.
–
PeakTemperature
50°CMax.
60°CMax.
DwellTime
3secMax.
5secMax.
LED Component
Lead Size
Diagonal
Plated Through
Hole Diameter
0.457x0.457mm
(0.018x0.018inch)
0.646mm
(0.05inch)
0.976to1.078mm
(0.038to0.04inch)
0.508x0.508mm
(0.00x0.00inch)
0.718mm
(0.08inch)
1.049to1.150mm
(0.041to0.045inch)
Note:RefertoapplicationnoteAN107formoreinformationonsolder-
ingLEDcomponents.
Figure 8. Recommended wave soldering profile.
LAMINAR WAVE
HOT AIR KNIFE
BOTTOM SIDE
TOP SIDE OF
TURBULENT WAVE
FLUXING
PREHEAT
0
10
20
30
50
100
150
200
250
30
40
50
TIME – SECONDS
T
°
C
60
70
80
90
100
CONVEYOR SPEED = 1.83 M/MIN (6 FT/MIN)
PREHEAT SETTING = 150
C (100
C PCB)
SOLDER WAVE TEMPERATURE = 245
°
C
AIR KNIFE AIR TEMPERATURE = 390
C
AIR KNIFE DISTANCE = 1.91 mm (0.25 IN.)
AIR KNIFE ANGLE = 40
°
SOLDER: SN63; FLUX: RMA
NOTE: ALLOW FOR BOARDS TO BE
SUFFICIENTLY COOLED BEFORE EXERTING
MECHANICAL FORCE.
For product information and a complete list of distributors, please go to our web site:
www.avagotech.com
Avago, Avago Technologies, and the A logo are trademarks of Avago Technologies in the United States and other countries.
Data subject to change. Copyright 2005-2008 Avago Technologies. All rights reserved.
Obsoletes 5989-4254EN
AV02-1556EN
- October 13, 2008