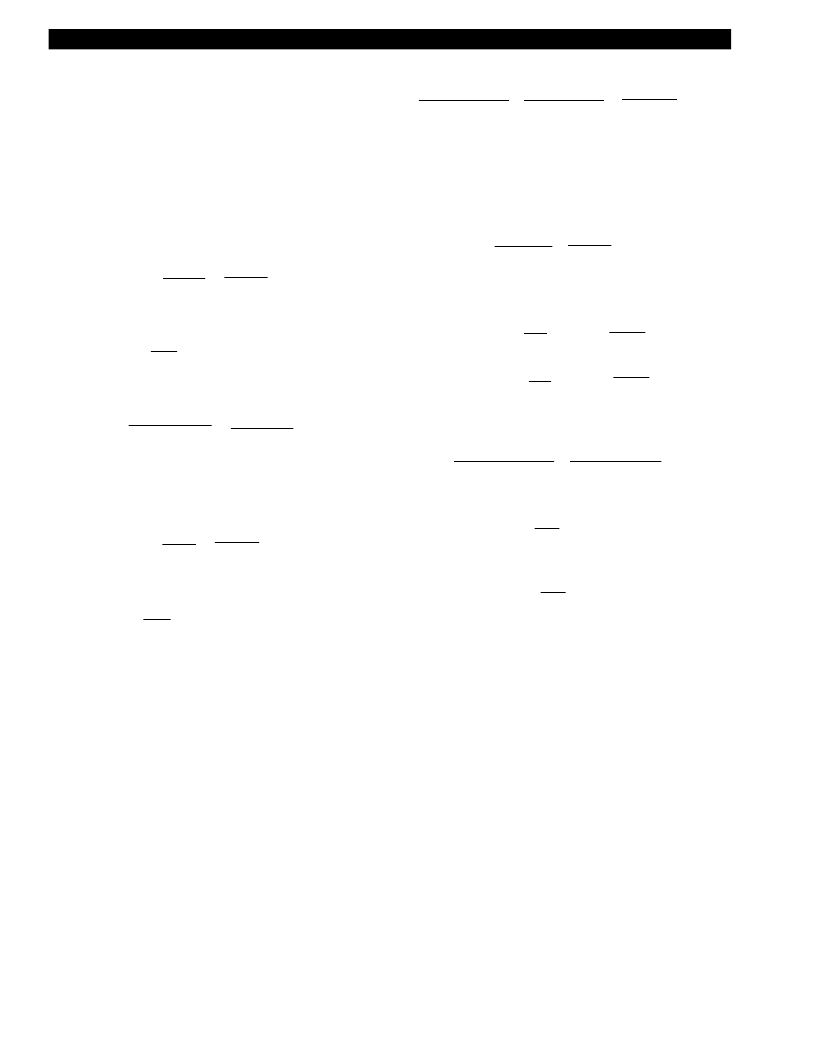
than ±165mV. Repeating step 2a, we select four (4)
1200μF/10V Sanyo GX output capacitors.
Step 3: Duty Cycle, Switching Frequency, T
ON
& T
OFF
Duty Cycle
V
OUT
/ V
IN.
D = 2.0V / 5V = 40% for 2V output.
D = 3.3V / 5V = 66% for 3.3V output.
Select 200kHz Switching Frequency (F
SW
).
Step 3a: Calculate On-Time for 2V Output
T
ON
=
=
= 2μs
Calculate Off-Time:
T
OFF =
= 5μs - 2μs = 3μs.
Select the C
OFF1
capacitor in order to set the Off-Time:
C
OFF1
=
=
= 750pF.
A standard C
OFF1
capacitance value of 680pF can be used.
The 3980 factor is a characteristic of the CS5132.
Step 3b: Calculate On-Time for 3.3V Output
T
ON
=
=
= 3.3μs
Calculate Off-Time:
T
OFF
=
- T
ON
= 5μs D 3.3μs = 1.7μs.
Select C
OFF2
to be 390pF.
Step 4: Output Inductor
The inductor should be selected based on its inductance,
current capability, and DC resistance. Increasing the induc-
tor value will decrease output voltage ripple, but degrade
transient response. There are many factors to consider in
selecting the inductor including: cost, efficiency, EMI and
ease of manufacture. The inductor must be able to handle
the peak current at the switching frequency without satu-
rating, and the copper resistance in the winding should be
kept as low as possible to minimize resistive power loss.
There are a variety of materials and types of magnetic
cores that could be used for this application. Among them
are: ferrites, molypermalloy cores (MPP), amorphous and
powdered iron cores. We will use a powdered iron core.
Iron powdered cores are very suitable due to their high sat-
uration flux density and have low loss at high frequencies,
a distributed gap and exhibit very low EMI.
Calculate Inductor Value:
L=
=
=
=1.2μH.
Step 4a: Select 2% Ripple on 2V Output
D
V
OUT
= 2%
′
2V = 40mV
The maximum allowable Inductor Ripple Current for a 2%
ripple on the 2V output is:
D
I
L
=
=
= 7.3A,
which corresponds to the following maximum Inductor
Peak and Valley currents:
)
= 16A +
(
2
I
L(PEAK)
= I
OUT
+
(
)
= 19.6A,
I
L(VALLEY)
= I
OUT
-
(
)
= 16A -
(
)
= 12.4A.
The selected 1.2μH inductor yields the following ripple
current:
(V
IN
- V
OUT
)
′
D
F
SW
′
L
D
I
L
=
=
= 5A.
The maximum inductor peak current becomes:
I
L(PEAK)
= 16A +
= 16A + 2.5A = 18.5A.
The inductor valley current becomes:
I
L(VALLEY)
= 16A -
= 16A - 2.5A = 13.5A.
The above values are well within the maximum allowable
inductor peak and valley currents for a 2% output voltage
ripple.
Select Toroid Powdered Iron Core, low cost, low core loss-
es at 200kHz, low EMI.
Select XFMRS Inc, XF0016-VO4 1.2μH inductor with R
DC
=
0.003 typical, 0.008 maximum.
Step 4b: Select 2% Ripple on 3.3V Output
Repeating Step 4a for the 3.3V output, we find 3.5μH is a
suitable value for this output.
Step 5: Input Capacitors
These components must be selected and placed carefully to
yield optimal results. Capacitors should be chosen to pro-
vide acceptable ripple on the input supply lines. Key speci-
fications for input capacitors are their ripple rating.
Step 5a: V
CC(CORE)
Buck Regulator Input Capacitors
The input capacitor C
IN
should also be able to handle the
5A
2
5A
2
(5V - 2V)
′
0.4
200kHz
′
1.2μH
7.3A
2
D
I
L
2
7.3A
2
D
I
L
40mV
5.5m
D
V
OUT
Total ESR
3V
′
6μs
15A
(5V-2V)
′
6μs
15A
(V
IN
- V
OUT
) t
TR
D
I
1
F
SW
0.66
200kHz
D
F
SW
5μs
′
0.6
3980
Period
′
(1-D)
3980
- T
ON
1
F
SW
0.40
200kHz
D
F
SW
Application Information: continued
12
C