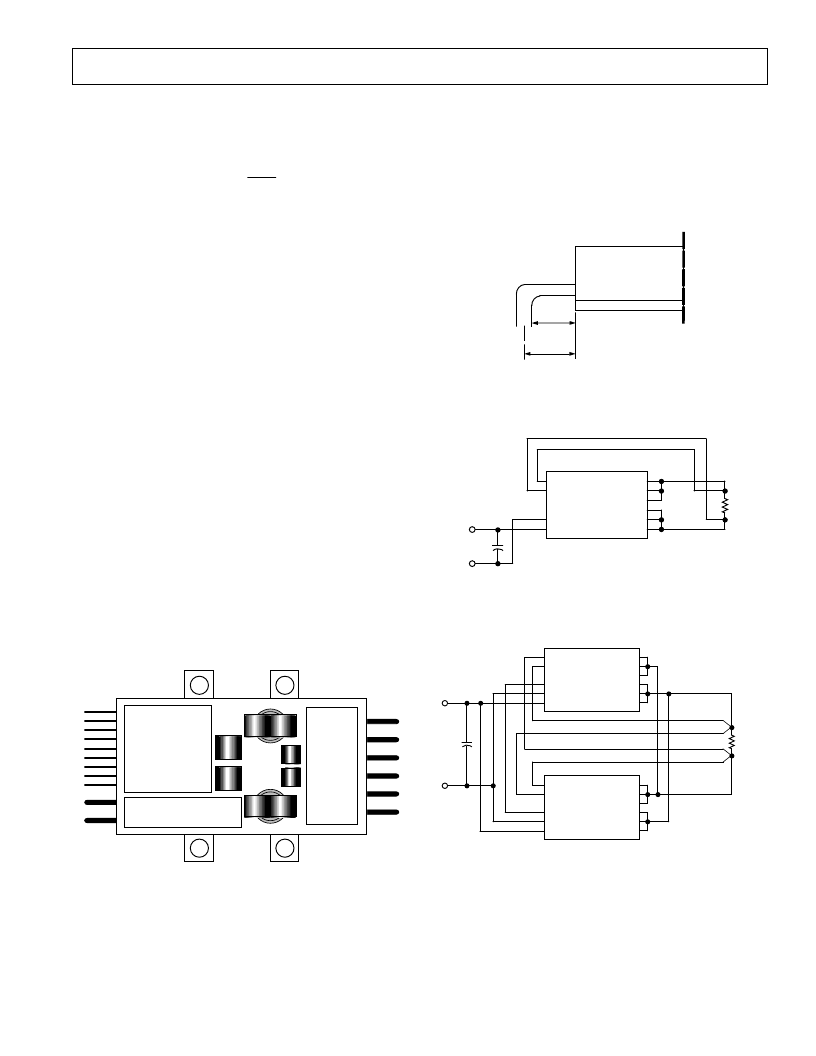
ADDC02808PB
REV. A
–19–
where
R(t)
is the probability of a device not failing prior to some
time t.
If we substitute
λ
= 1/MTBF in the above formula, then the
expression becomes
R
(
t
)
=
e
–
t
MTBF
This formula is the correct way to interpret the meaning of
MTBF.
If we assume t = MTBF = 1,000,000 hours, then the probability
that a power supply will not fail prior to 1,000,000 hours of use
is e
–1
, or 36.8%. This is quite different from saying the power
supply will last 1,000,000 hours before it fails. The probability
that the power supply will not fail prior to 50,000 hours of use is
e
–.05
, or 95%. For t = 10,000 hours, the probability of no failure
is e
–.01
, or 99%.
Temperature and Environmental Factors:
Although the
calculation of MTBF per MIL-HDBK-217 is a detailed process,
there are two key variables that give the manufacturer signi-
ficant leeway in predicting an MTBF rating. These two vari-
ables are temperature and environmental factor. Therefore, for
users to properly compare MTBF numbers from two different
manufacturers, the environmental factor and the temperature
must be identical. Contact the factory for MTBF calculations
for specific environmental factors and temperatures.
MECHANICAL CONSIDERATIONS
When mounting the converter into the next higher level assem-
bly, it is important to insure good thermal contact is made be-
tween the converter and the external heat sink. Poor thermal
connection can result in the converter shutting off, due to the
temperature shutdown feature (Pin 9), or reduced reliability for
the converter due to higher than anticipated junction and case
temperatures. For these reasons the mounting tab locations
were selected to insure good thermal contact is made near the
hot spots of the converter which are shown in the shaded areas
of Figure 42.
Figure 42. Hot Spots (Shaded Areas) of DC/DC Converter
The pins of the converter are typically connected to the next
higher level assembly by bending them at right angles, either
down or up, and cutting them shorter for insertion in printed
circuit board through holes. In order to maintain the hermetic
integrity of the seals around the pins, a fixture should be used
for bending the pins without stressing the pin-to-sidewall seals.
It is recommended that the minimum distance between the
package edge and the inside of the pin be 100 mils (2.54 mm)
for the 40 mil (1.02 mm) diameter pins; 120 mils (3.05 mm)
from the package edge to the center of the pin as shown in
Figure 43.
0.100"
(2.54mm)
0.120"
(3.05mm)
Figure 43. Minimum Bend Radius of 40 Mil (1.02 mm)
Pins
C1
+28VDC
28RTN
1
2
10
11
17
16
15
14
13
12
ADDC02808PB
PS1
RLOAD
NOTE: VALUE OF C1 IS DEPENDENT ON SOURCE IMPEDANCE.
REFER TO SECTION ON SYSTEM INSTABILITY CONSIDERATIONS.
Figure 44. Typical Power Connections and External Parts
for Converter
+SENSE PS1
+SENSE PS2
–SENSE PS1
–SENSE PS2
RLOAD
V
OUT
+
V
OUT
–
1
2
8
10
11
17
16
15
14
13
12
ADDC02808PB
1
2
8
10
11
17
16
15
14
13
12
ADDC02808PB
PS2
PS1
I SHARE
C1
+28VDC
28RTN
NOTE: VALUE OF C1 IS DEPENDENT ON SOURCE IMPEDANCE.
Figure 45. Typical Connections for Paralleling Two
Converters